11 - ShapeMetriX Integration
1.0 Introduction
This tutorial demonstrates RocSlope3’s ShapeMetriX Geometry and Joint Import options. It also demonstrates how the integration and interoperability of ShapeMetriX and RocSlope3 streamlines the 3D block stability analysis workflow, from data acquisition in the field. It helps to determine each block's stability and predict failure locations and magnitudes. The tutorial will help you become familiar with importing ShapeMetriX 3D Models to generate a RocSlope3 model and structures (i.e. joints) to perform a 3D block stability analysis in RocSlope3.
Topics Covered in this Tutorial:
- Importing 3D Model from ShapeMetriX
- Importing Measured Joints from ShapeMetriX
- Results Interpretation
Finished Product:
The finished product of this tutorial can be found in the Tutorial 11 ShapeMetriX Integration folder, located in the Examples > Tutorials folder in your RocSlope3 installation folder.
2.0 ShapeMetriX 3D Model Generation and Structural Mapping
ShapeMetriX is a comprehensive software suite designed for geologic mapping and geometric analysis, equipped with an advanced 3D model generator. It is ideal for creating 3D models of rock surfaces, rock slopes, tunnel faces and walls, etc. using digital imagery or by importing 3D datasets (E57 laser scanner or OBJ data) and performing fast, detailed, non-contact geological mapping and geometric assessment.
MultiPhoto, the first main component of ShapeMetriX, uses multiple overlapping images from standard drones and handheld cameras, including smartphones as input and generates 3D models by estimating the 3D structure of a scene from a set of 2D images using the Structure from Motion (SfM) process. Additionally, MultiPhoto includes standard and constrained referencing features that reference the 3D model to a higher-level coordinate system using externally surveyed Ground Control Points (GCP).
3D Model Generation and Referencing are discussed in more detail in ShapeMetriX Tutorial 1 – 3D Model Generation and Tutorial 2 – Standard and Constrained Referencing Using Ground Control Points.
Analyst, the second main component of ShapeMetriX, is a convenient tool designed for visualizing and assessing 3D models. Analyst features a fast and detailed visualization of single, multiple and merged 3D models and allows users to perform geometric measurements like dip directions and dip angles, lineaments, rock bridges (non-persistent elements), areas, distances, point locations, occurrences (water, single events), partitioning of areas (lithology and homogeneous areas), and many more, directly on a 3D model. Analyst also includes attributes like:
- Grouping measurements into Structure Sets
- Semi-automatic trace detection
- Automatic joint set clustering
- Orientation of areas and traces including stereographic projection and statistics
- Defining scanlines and mapping regions
- Lithologic region and homogenous area mapping
These help to streamline the geological and geotechnical assessment of rock faces or terrains across various scales, such as open pit mines, tunnel faces, rock slopes, drift faces, caverns, quarries, laboratory samples, and constructions like dams.
Geometric Measurements and Structural Mapping in ShapeMetriX are discussed in more detail in Tutorial 3 – Geometric Measurement and Structural Mapping.
3.0 3D Model
The model used in this tutorial is a 15m high and approximately 90m long bench face from an open pit mine with a large number of measured joint surfaces and traces of known orientation, size, and location. The 3D model is generated in ShapeMetriX’s MultiPhoto tool using 49 aerial images, and the structural mapping is performed in ShapeMetriX’s Analyst tool using semi-automatic joint trace and surface mapping features.
The 3D model geometry and the mapped joints data are exported as RocSlope3 readable files (.3grs for model geometry and .3gdps for joint data). These exported files will be used as input files in RocSlope3 and can be found in the Examples > Tutorials > Tutorial 11 ShapeMetriX Integration folder in your RocSlope3 installation folder.
3.1 Project Settings
Open RocSlope3. You will see a blank workspace.
Our first step is to configure the analysis parameters for the model in the Project Settings.
- Select Analysis > Project Settings or click on the Project Settings
icon in the toolbar.
- Select the Units tab.
- Set Units = Metric, stress as MPa and keep everything else as default.
- Select the Analysis tab. Ensure:
- Design Factor of Safety = 1.0
- Successive Failure = ON
- Click OK to save the settings and close the dialog.
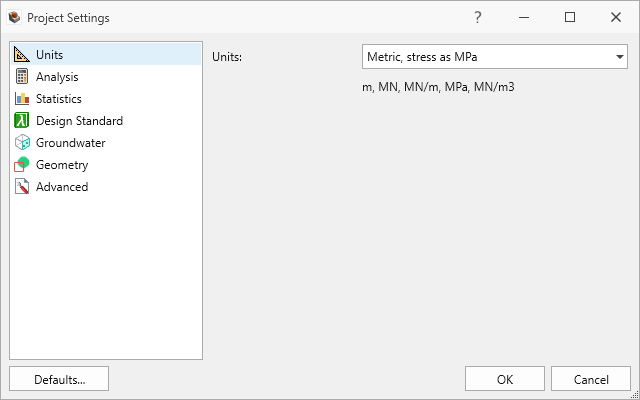
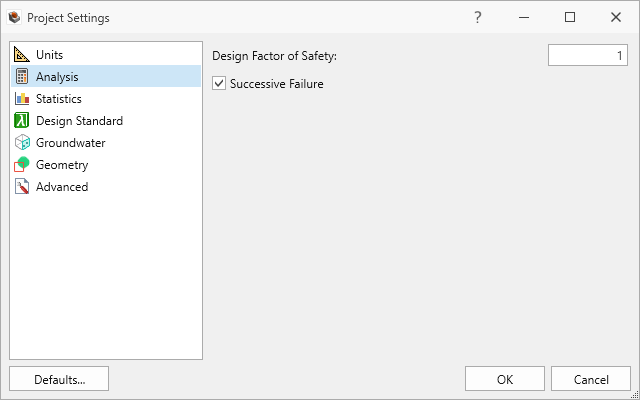
3.2 Import Geometry
To import the Bench Face geometry into RocSlope3:
- Select Geometry > Import/Export > ShapeMetriX Import
- In the Surface Reconstruction dialog, click Browse
, select the Blocky Bench Geometry.3grs file in the Tutorial 11 ShapeMetriX Integration folder (located in your installation folder) and click Open.
- Ensure that the Surface Reconstruction parameters are as follows:
- Density of Voxels = 100
- Number of Buffer Voxels = 1
- Depth of Extrusion = 5
- Click OK to complete the geometry import.
The geometry file will be imported, and surface reconstruction will be performed automatically. The preview of the extruded volume will be displayed in the dialog.
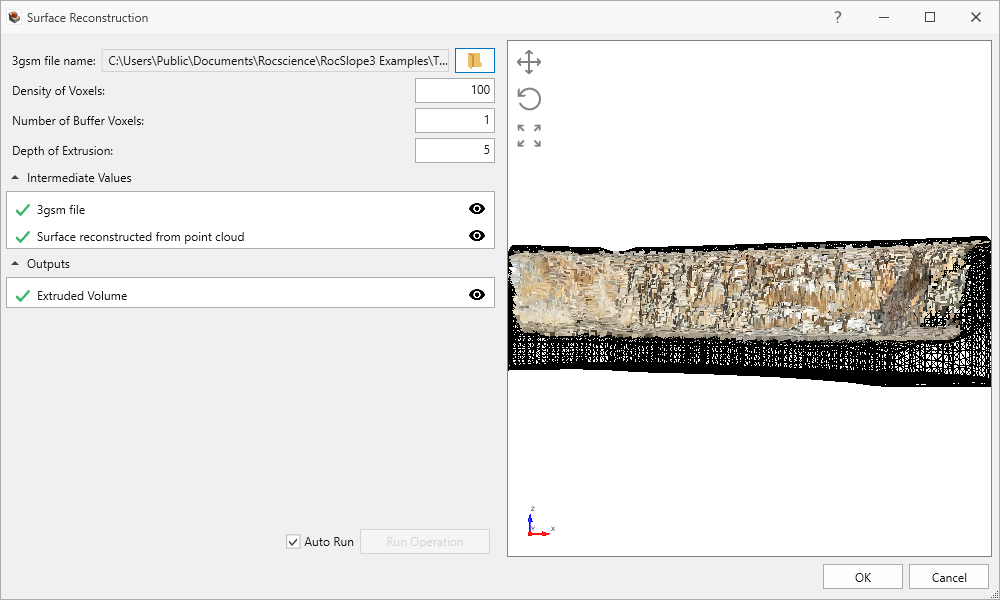
Density of voxels controls how dense the resulting mesh will be. Increasing the density will result in a denser mesh triangulation.
Number of Buffer Voxels controls how far beyond the extents of the input point cloud the surface is extrapolated. Increasing the number will cause the surface to be extended further. Increasing this value can be useful to fill gaps in sparse input data, though at large numbers the extrapolated regions may not accurately reflect the input data.
Tip: Auto running the extruded volume generation from reconstructed surface can be turned on and off by selecting or deselecting the Auto Run checkbox in the Surface Reconstruction dialog.
The geometry is imported into RocSlope3 and added to the Visibility Tree. Click the Imported ShapeMetriX Geometry entity in the Visibility Tree. Notice in the Properties pane (below the Visibility pane) that the entity is imported as a closed Volume.
3.3 Setting the Volume as External
We now have to set the Volume entity as External to create a valid external geometry for modelling.
To set the external geometry from the volume entity:
- Select the Imported ShapeMetriX Geometry volume entity in the Visibility Tree. The entity is highlighted in the 3D View.
- Select Geometry > Set as External
The selected volume is now defined as the External volume. In this model, there is only one (1) Material Volume assigned with the Material 1 material property.
3.4 Defining Joint Properties
To define joint properties:
- Navigate to the Joints workflow tab
- Select Joints > Define Joint Properties or click on the Define Joint Properties
icon in the toolbar.
- Select Joint Property 1 from the list on the left side of the dialog. Enter the following properties for Joint Property 1:
- Under the Strength tab:
- Strength Type = Mohr-Coulomb
- Cohesion = 0 MPa
- Phi = 30 deg
- Override by Material = OFF
- Waviness = 0 deg
- Under the Water Parameters tab:
- Water Pressure Method = Dry
- Under the Strength tab:
- Click OK to save and close the Define Joint Properties dialog.
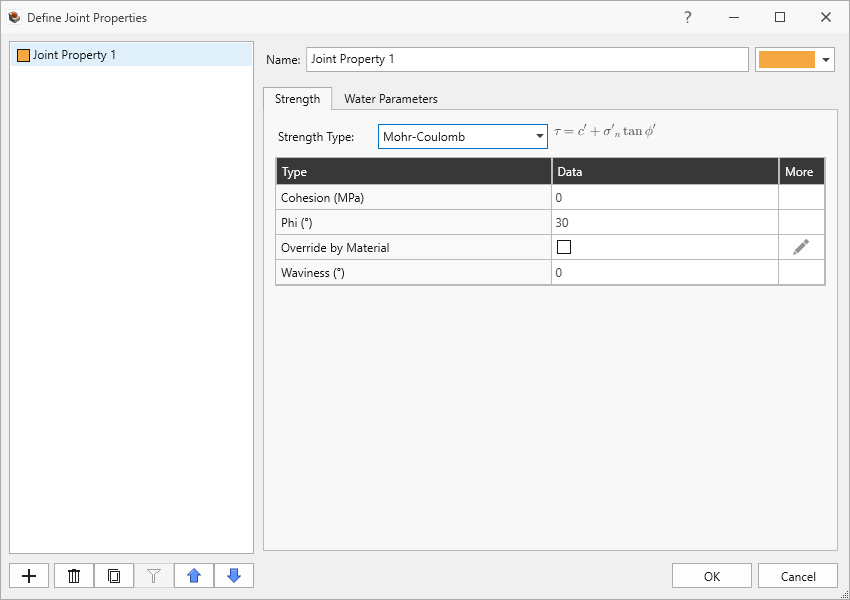
3.5 Importing Measured Joints
We will be defining the joints using measured orientation data from a ShapeMetriX structural mapping file (.3gdps).
To define measured joints:
- Ensure the Joints workflow tab
is still active.
- Select Joints > Define Measured Joints
or click on the Define Measured Joints
icon in the toolbar.
- Select Shear Strength = Use Joint Properties. We will be assigning the Joint Property 1 we defined earlier.
- Click Import ShapeMetriX
- In the Open dialog, select the Blocky Bench Joints.3gdps file from the Tutorial 11 ShapeMetriX Integration folder and click Open.
- Notice that Joint Orientations (Dip and Dip Directions), Locations (X, Y and Z) and Radius (Persistence) are imported. Joint Property 1 is also assigned to all the joints as their Joint Property.
- Click OK to save the inputs, exit the Define Measured Joints dialog and add the joints to the model.
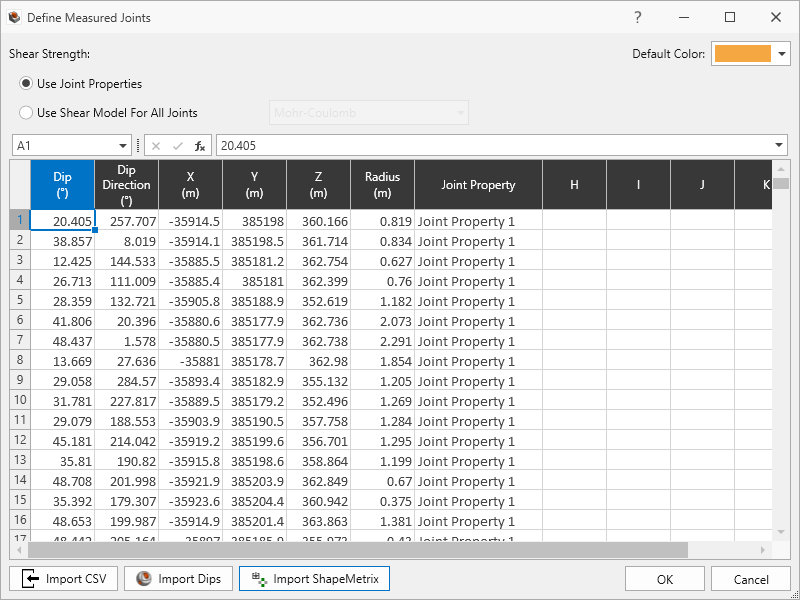
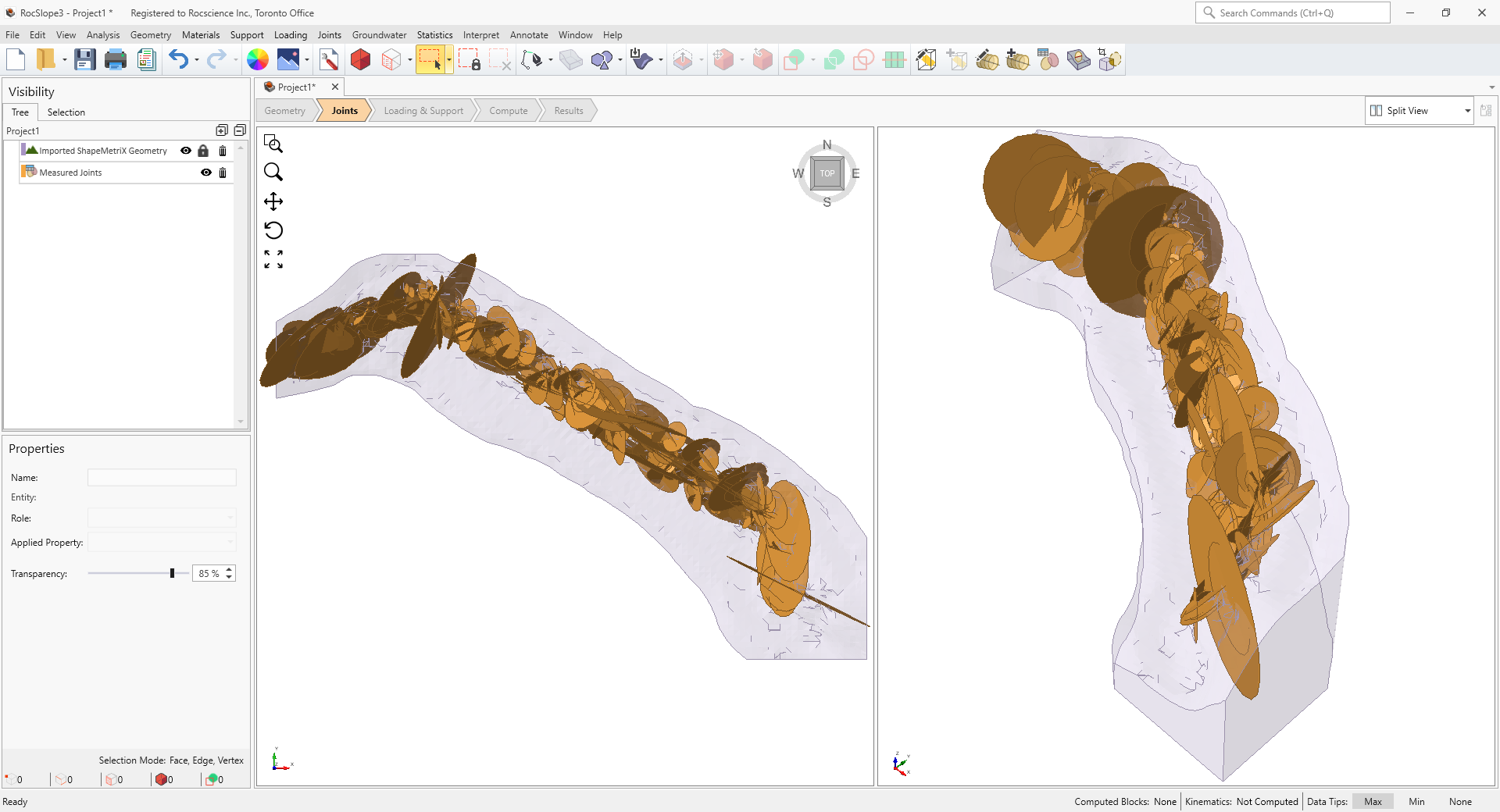
4.0 Compute
RocSlope3 has a two-part Compute process.
4.1 Compute Blocks
The first step is to compute the blocks which may potentially be formed by the intersection of joints with other joints and the intersection of joints with the free surface.
To compute the blocks:
- Navigate to the Compute workflow tab
- Select Analysis > Compute Blocks or click the Compute Blocks
icon in the toolbar.
As compute is run, the progress bar reports the compute status. Once compute is finished, the Results node is added to the Visibility Tree and All Valid Blocks are shown in the 3D View. The Results node consists of the collection of valid blocks and the socketed slope. The original External and Measured Joints visibility is turned off.
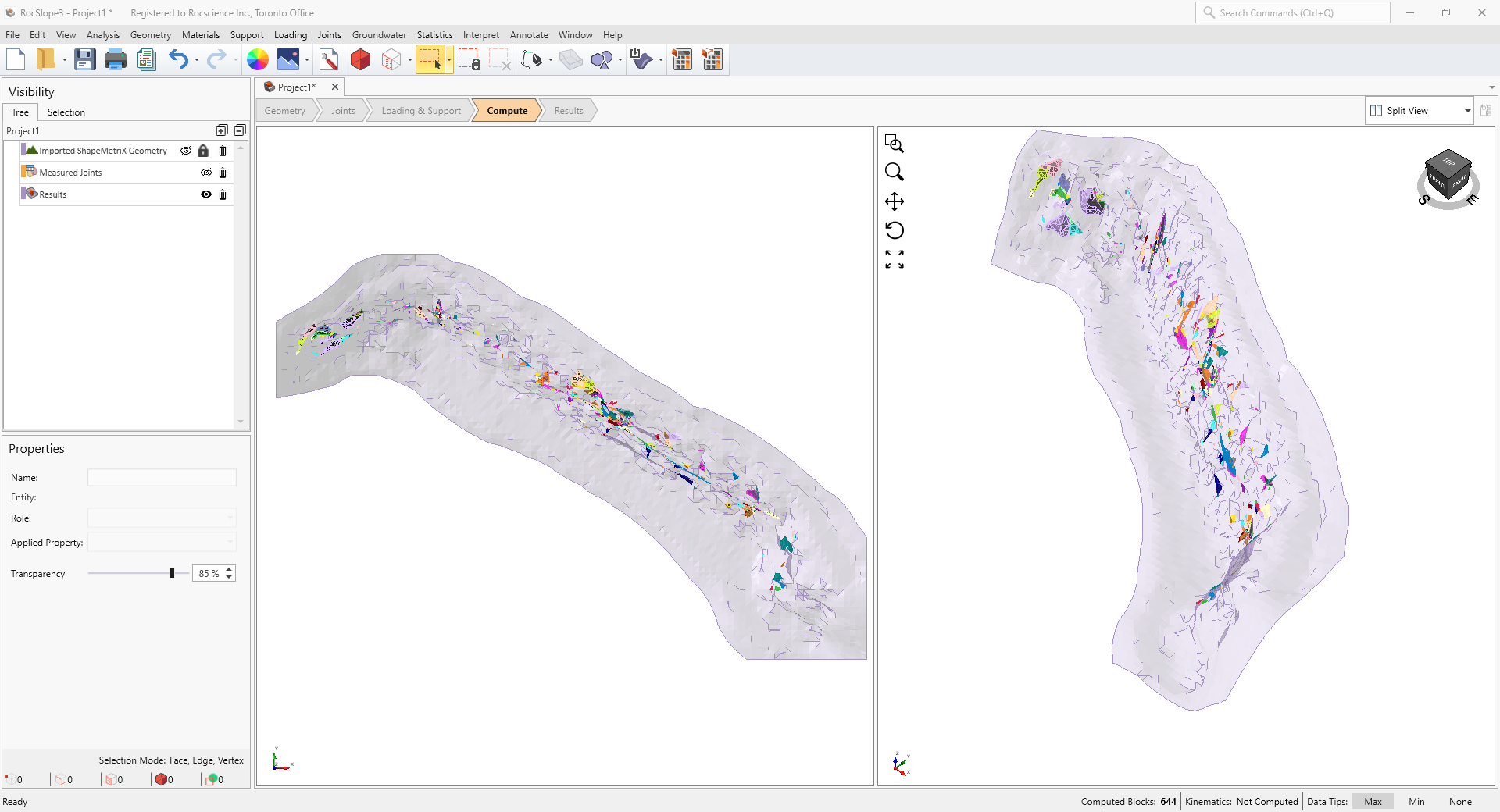
Once compute is finished, the blocks are coloured according to the Block Color option (Random Colors) set in the Results node's Property pane.
Compute Blocks only determines the geometry of the blocks. In order to obtain other information such as the factor of safety, Compute Kinematics needs to be run.
4.2 Compute Kinematics
The second and final compute step is to compute the removability, forces, and factor of safety for each of the valid blocks.
To compute the block kinematics:
- Ensure that the Compute workflow tab
is still the active workflow.
- Select Analysis > Compute Kinematics or click the Compute Kinematics
icon in the toolbar.
As compute is run, the progress bar reports the compute status. By default, after Compute Kinematics is run, only Removable Blocks are shown.
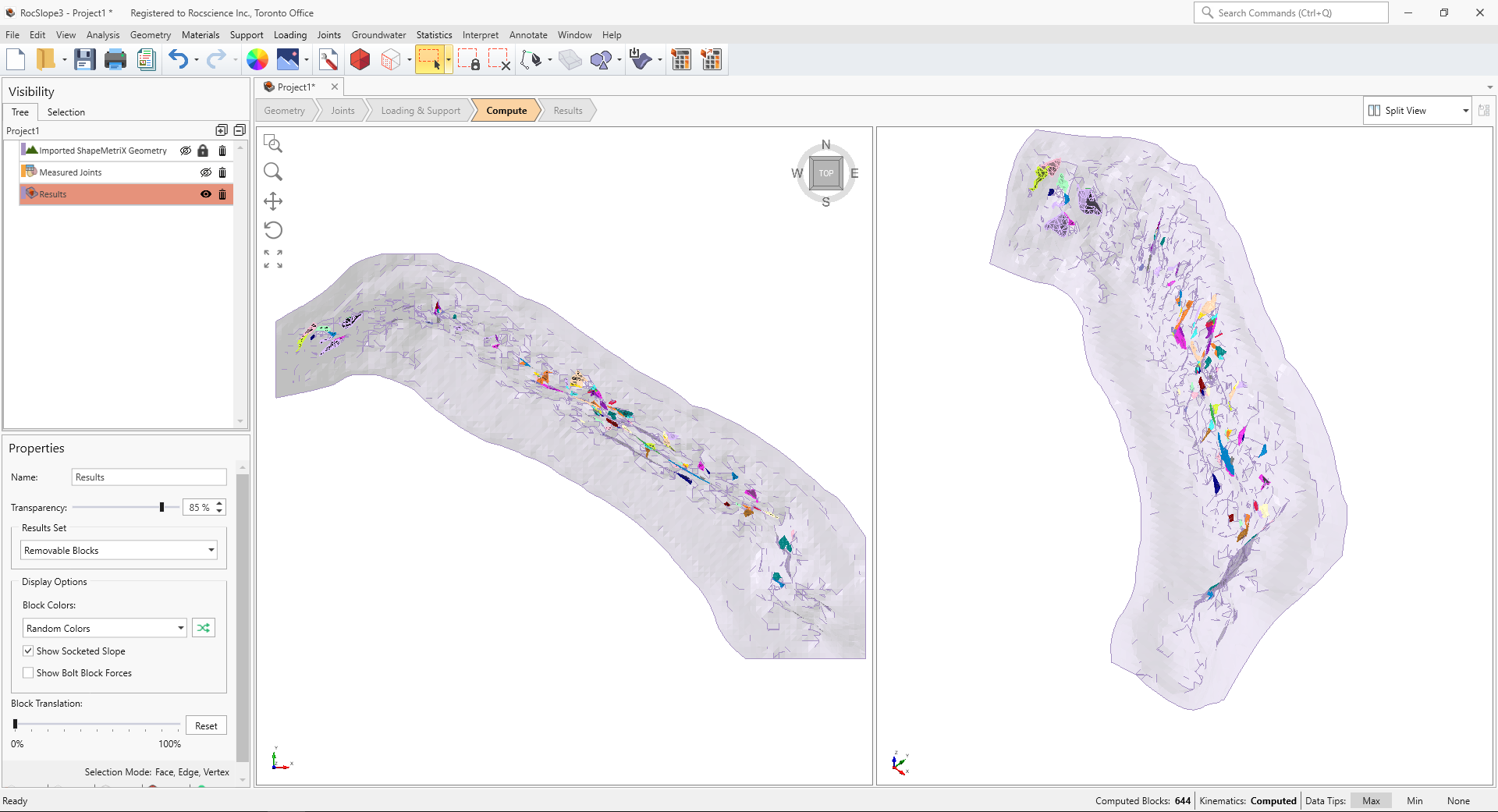
In a Successive Failure mode of analysis, several Failure Iterations may be performed. In the first Failure Iteration, only immediately removable daylighting blocks are analyzed. Any blocks which have a factor of safety less than the Design Factor of Safety (set in Project Settings) is considered "failed". These blocks are also known as "key blocks". The stability of key blocks controls the global stability of the slope. As key blocks fail and are detached from the slope, potential constraints in joint faces (in regard to removability and valid sliding direction) are removed and become free faces which no longer support the block or provide shear resistance to sliding. As such, the failure proceeds in a successive manner. See the Analysis topic for more information on Successive Failure.
5.0 Interpreting Results
Once both blocks and kinematics are computed, all block results can be viewed in a grid format.
5.1 Block Information
To view all block results:
- Navigate to the Results workflow tab
- Select Interpret > Block Information or click on the Block Information
icon in the toolbar.
Visualizing blocks can be difficult when the slope extents are large compared to the block extents.
To zoom into all blocks:
- Select Interpret > Zoom to All Blocks
The Block Information pane shows the collection of blocks according to the Results Set settings. The Results Set shown can be selected in the Results tab of the Display Options, or the Properties pane for the Results Node. In this case, only Removable Blocks are colored and listed in Block Information.
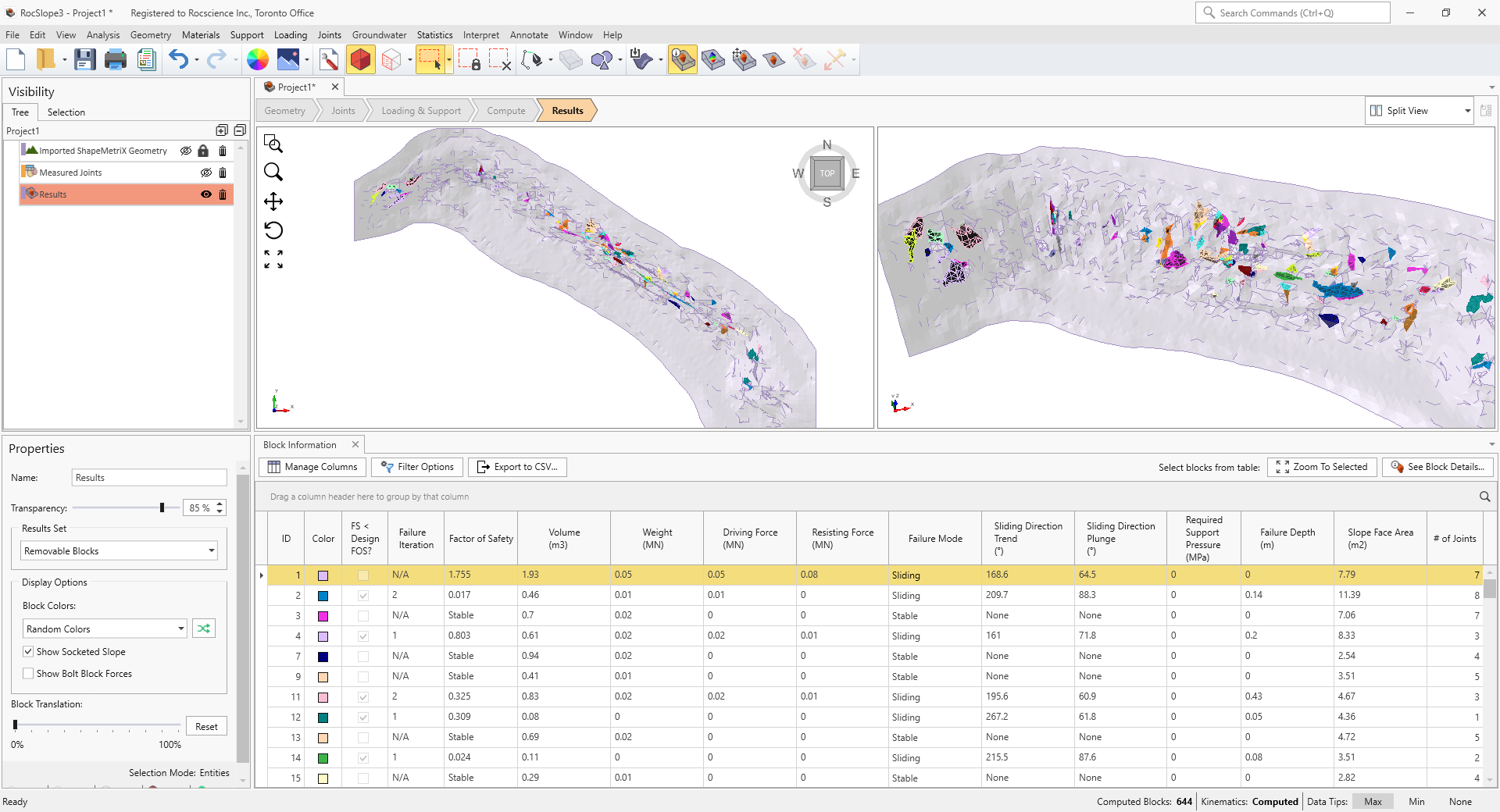
644 blocks are computed, as displayed in the Status Bar at the bottom right of the RocSlope3 window. 168 valid blocks are formed, and 112 blocks are Removable. 54 of these blocks have a Factor of Safety less than the Design Factor of Safety (<1.0).
Tip: The number of Valid, Removable and Failed blocks can be viewed by clicking the Filter icon in Block ID column in Block Information pane while the corresponding Results Set is selected.
In the case of Successive Failure, it may be more beneficial to only colour the failed blocks. Failed blocks are blocks which have a factor of safety less than the Design Factor of Safety.
To colour Failed Blocks Only:
- Select the Results node from the Visibility Tree.
- In the Results node Properties pane, set Results Set = Failed Blocks (FS < Design FS).
Failed Blocks Only are now coloured according to Random Colors.
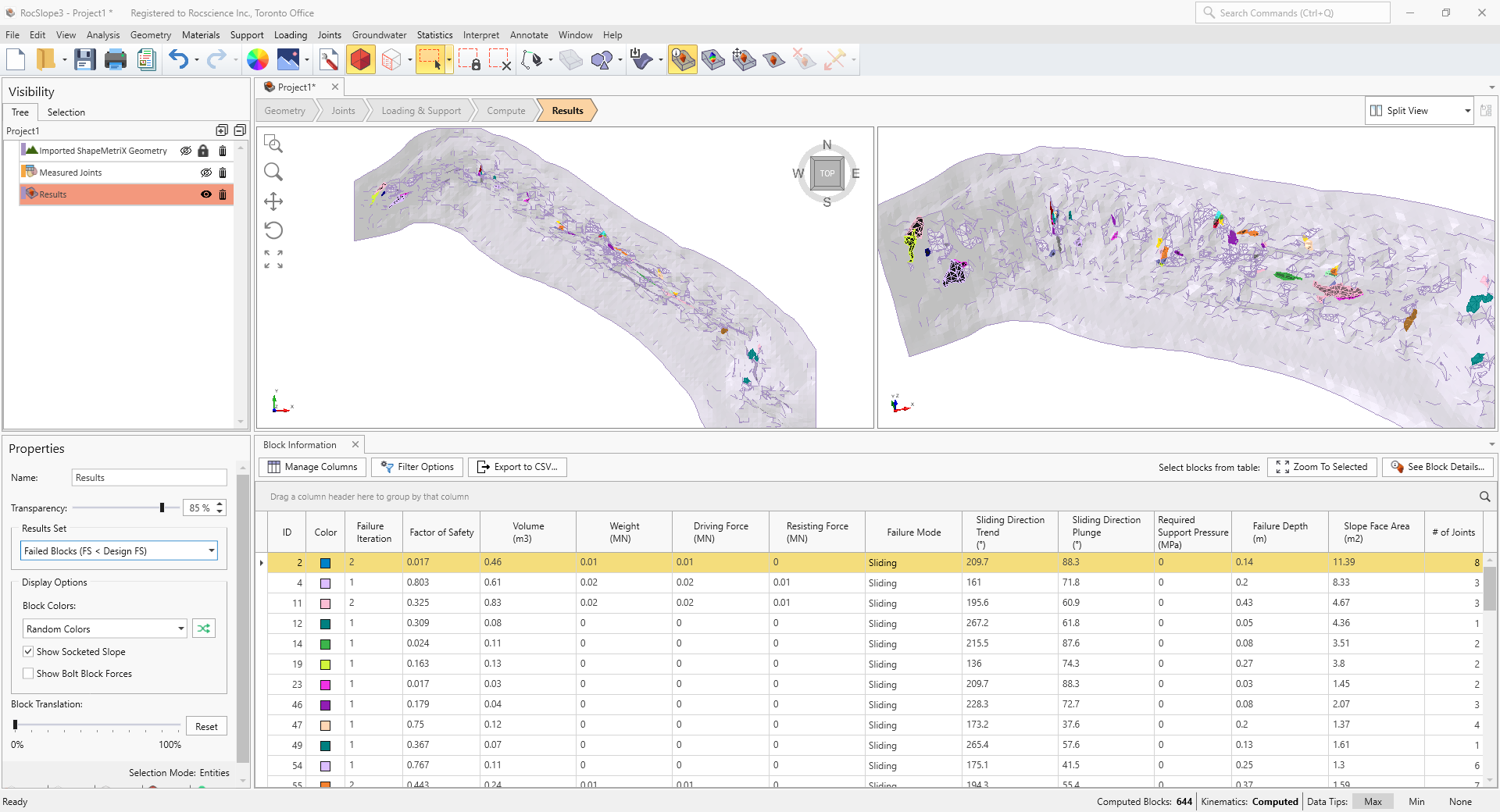
Note that the Failure Iteration column is visible for a Successive Failure analysis. The Failure Iteration indicates the step in which the block fails. It is not a true representation of the complex unraveling mechanism, but rather for notation and filtering.
Notice that 40 blocks are immediately unstable and fail in Failure Iteration = 1. In other words, they are the key blocks. On the other hand, 10 blocks are failing in Failure Iteration = 2, 3 blocks are failing in Failure Iteration = 3 and 1 block is failing in Failure Iteration = 4.
See Tutorial 5 – Successive Failure for more information on the Successive Failure phenomenon and how it is utilized in RocSlope3.
5.2 Detailed Block Information
To see the detailed information for a given block:
- Select the row for the block of interest in the Block Information pane. For this example, we will select Block ID = 4 from the rows of the Block Information (or graphically, by clicking the Block in the 3D View).
- Click the See Block Details
button at the top right of the Block Information pane.
The Detailed Block Information dialog shows the 3D model of the Block, general block information as well as detailed information for Joints, Joint Line of Intersection, and Block Vertices.
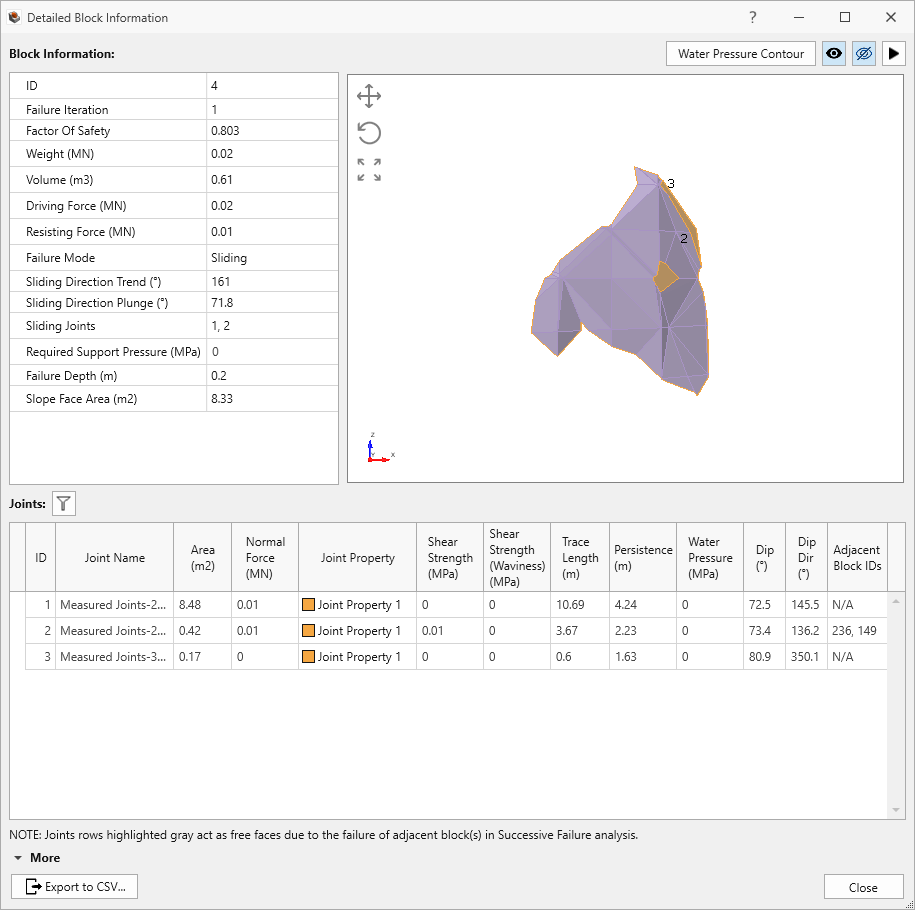
Now let’s look at Block Details of another block.
- Select the Block ID = 11 from the rows of the Block Information (or graphically, by clicking the Block in the 3D View).
- Click See Block Details
- Notice that the block with Block ID = 11 is failing in Failure Iteration = 2. Note that the Joint = 2 is highlighted grey since it is treated as a free face due to the detachment of the adjacent in the Successive Failure analysis.
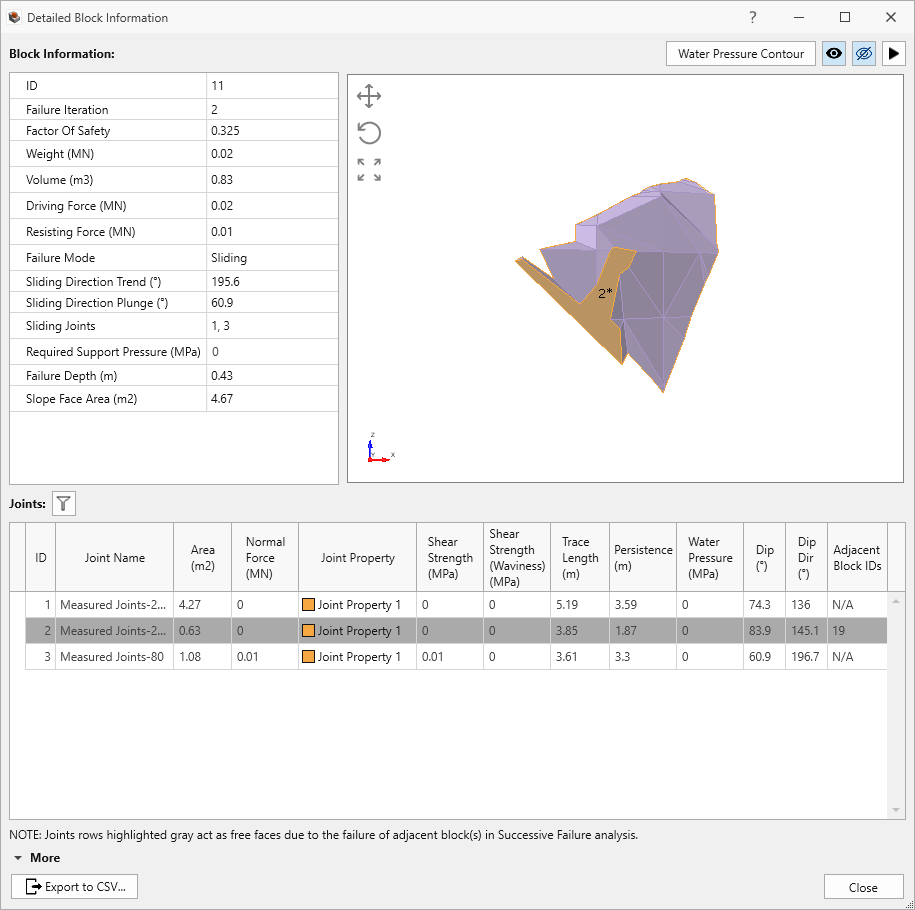
This concludes Tutorial 11.