Mesh Quality
The Mesh Quality option allows you to detect and troubleshoot problems which may exist with the finite element mesh. If you are experiencing problems with your analysis (e.g. non-convergence of solution, aborted computation, warning or error messages during compute, unusual analysis results), then it is advisable to check for mesh problems with the Mesh Quality option.
Overview
In a finite element mesh, it is generally desirable to avoid elements of high aspect ratio (i.e. long "thin" elements). The presence of such elements can have adverse effects on the analysis results.
- In general, such elements can influence analysis results, and lead to misleading and inaccurate results, which are dependent on the mesh.
- In extreme cases, such elements may even be responsible for non-convergence of the finite element solution, and the analysis will be aborted.
In order to help the user to determine the "quality" of a finite element mesh, RS3 can locate and highlight elements in a mesh, which are deemed to be of "poor" quality, according to user-definable criteria. This is done with the Mesh Quality option.
Mesh Quality
In order to locate and highlight poor quality elements in a mesh:
- Select the Mesh
workflow tab.
- Ensure a mesh has already been generated in the model.
If not, generate a mesh with the Mesh Settingsor Mesh
option. See the page for more details.
- Select the Mesh Quality
option from the toolbar or the Mesh menu.
- The Mesh Quality Metrics dialog should appear.
Define the mesh quality criteria in the dialog. See the Mesh Quality Metrics section below for details.
- Select Apply to view any poor quality elements based on the defined criteria. Make sure the Draw checkbox is on. If poor quality elements exist, they will be highlighted (see Figure 1 below).
In most cases, you will need to zoom in to get a good view of the highlighted poor quality elements, and determine what may be the cause of the problem. - Select OK to save and exit the dialog.
The created criterion will be added under the Visibility Tree as an entity named “mesh quality”. To edit it, expand the entity and select the pencilto modify in the dialog.
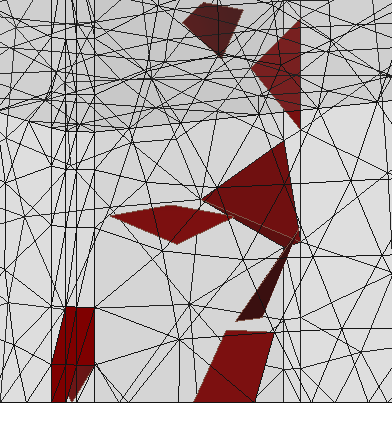
Mesh Quality Metrics
The Mesh Quality Metrics dialog allows you to define the mesh quality criteria. The metrics evaluates the mesh quality using a shape quality query (Qs), which is calculated as:
The shape quality query (Qs) ranges from 0 to 1. Qs = 1 means the tetrahedron is in the best shape, where its all four triangles are equilateral. Qs = 0 is the worst, which means the tetrahedron is excessively distorted that it becomes a triangular flat face or even a line. See Figure 2 below.
![]() | ![]() |
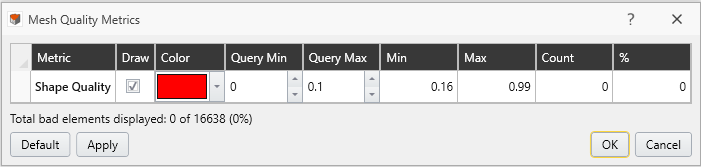
In the Mesh Quality Metrics dialog (see Figure 3 above), specify the shape quality query (Qs) range by defining a Query Min as the lower bound, and Query Max the upper bound. The following parameters will then be updated. The Min and Max provide the minimum and maximum query value found in the model within the defined range, respectively. The Count refers to the number of elements found within the defined range. The % refers to the percentage of the targeted number of elements among all elements in the model. The
Default button sets a default criterion of the query range between 0 and 0.1 to detect poor-quality elements.
- To identify the poor-quality elements, the range should be closer to 0. However, you can also specify a higher range to identify the good-quality elements, or any other interested ranges.
- If Query Min = Query Max, it will only select the element that have quality exactly at the value.
Display Mesh Quality
Enable the Draw checkbox allows you to display the elements within the defined query range in the viewport. You can choose a Color for the displayed elements. A footnote “Total bad elements displayed: ‘targeted #’ of ‘total #’ (percentage).” will be updated in the dialog.
The Apply button displays the elements in the viewport, which are highlighted in the defined Color (see Figure 1 above).
Reasons for poor quality mesh elements
There are various reasons why poor quality mesh elements may be generated. Typically the problems are due to:
- Vertices which are very close to each other.
- Poorly graded mesh (for example, a finely discretized boundary immediately adjacent to, or close to, a coarsely discretized boundary, will often result in a poor quality mesh).
- The geometry of your model boundaries, for example, the relative distances between boundaries, or the way in which they intersect (e.g. nearly parallel boundaries which intersect at a very small angle).
Fixing a poor quality mesh
- If the problem is vertices which are very close to each other, then you may need to delete unnecessary vertices, or move vertices, so that they are further apart, or exactly coincident. If vertices were intentionally located very near to each other, and this is causing a problem, then you may want to consider modifying your geometry slightly, so that poor quality elements are not generated.
- If a poor grading is responsible for the poor mesh, then you may need to customize the mesh. This may involve use of the Mesh Settings or Mesh Refinement options.
- If the actual model geometry is responsible (e.g. very thin material layers), then various solutions might be appropriate, involving Mesh Settings or Mesh Refinement options, or modifying the boundaries slightly, so that the problem does not occur.