3D Finite Element Analysis of a Deep Excavation & Ground Response Evaluation
Significant ground movements due to deep surface excavations can seriously impact neighbouring infrastructure and utilities. When it comes to assessing the after-effects of excavations on adjacent infrastructure and planning fundamental mitigation measures, it’s of utmost importance to consider displacements due to deep excavations.
This case study demonstrates the capabilities of RS3’s 3D Finite Element Analysis as a primary design tool in the Observational Method (OM), during an excavation project for property development on Sydney’s North Shore.
Overview of the project
The project development is currently located at 88 Christie St, St Leonards, NSW. Images of the proposed development and aerial perspective of the site are shown in Figure 1.
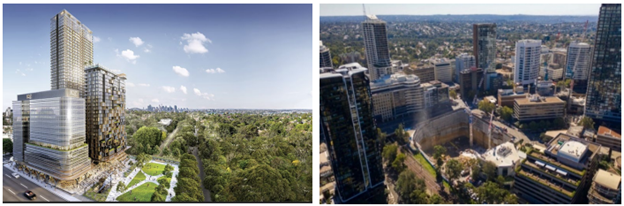
This development consists of two residential towers (maximum 47 storeys high) and a commercial tower (15 storeys) over a large retail area with 10 levels of the below-ground basement up to 43 m deep. The 8,000 m2 basement excavation extends to the Sydney Trains boundary and is situated along the major rail and road infrastructure shown in Figure 2.
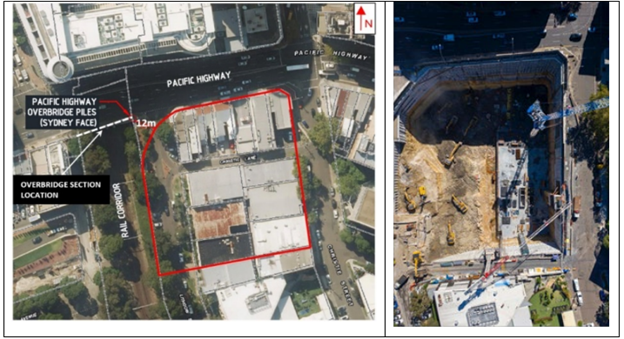
Adjacent infrastructure details
The site was surrounded by buried utilities, road and rail infrastructure, and buildings in the vicinity. The initial consideration for this development was about 14 m from CBD Rail Link which was planned earlier. This rail transport project consisted of two tunnels connecting south of the city, that added two more tracks on each side of the existing protection corridor, as shown in Figure 3.
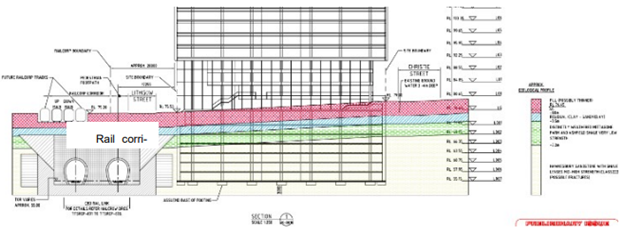
Excavation Design & Subsurface Conditions
The ground conditions were assessed using 52 boreholes, rock core samples, rock index strengths, borehole characteristics, and rock mass defects including joints and bedding partings.
There were specific restrictions for the development which included:
- A restriction on using anchor systems in the rail easement
- The construction and operations couldn’t affect the stability of the railway infrastructure
- A maximum displacement of 30mm on the Pacific Highway
- Monitoring of ground movements and track structures due to excavation was required
The following supports were installed:
- A contiguous concrete pile wall along with an anchored shotcrete wall
- Ground anchors within a 20m wide square buttress of rock on the south corner
- Ground anchors were placed across 20m in the north corner near the Pacific Highway railway bridge.
Excavation supports can be seen in Figure 4.
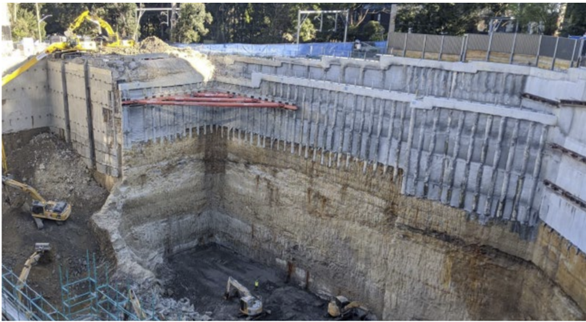
Impact Assessment
The impact assessment analyzed the effects of the development including basement excavation and building loads along with the correction of the natural stress field characterized by rock mass quality.
The initial numerical assessment of the rock mass responses and installed support was performed using RS2’s 2D Finite Element analysis and finite difference analysis using FLAC 3D. However, for a more detailed and realistic estimate of how existing infrastructure was affected due to construction, 3D Finite Element numerical modelling and analysis was carried out using RS3.
A shoring system with soldier piles and anchors was designed to control the ground surface deformation due to lateral soil pressure in the upper parts of the proposed excavation site and was calibrated using monitoring results from various deep excavations around Sydney.
The predicted ground movements from the 2D assessment using RS2 can be seen in Figure 5.
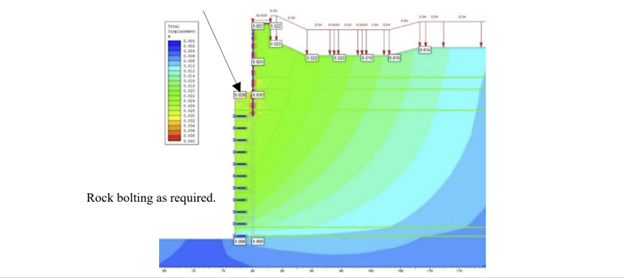
Basement Excavation using RS3
The investigation of the west railway wall suggested there could be a presence of weaker shale/laminate bands at about 40m depth. A temporary high stiffness anchor was installed to control ground movements due to wall deflection. While the bulk excavation was in progress, the automated inclinometer recorded horizontal sliding movement on the two shale bands which can be seen in Figure 6. The sliding movement was due to the release of in-situ stress within the sandstone causing the block of sandstone above the shale band to move more than predicted.
Initially, RS3 was used to calibrate a slice model to match the movement measured by the inclinometer. Further, the shale band was modelled as a ubiquitous joint model with Mohr-Coulomb parameters. After the model was calibrated, several options were tested to reduce the movement and provide additional support to the wall and ensure that the railway track wasn’t impacted by the movements.
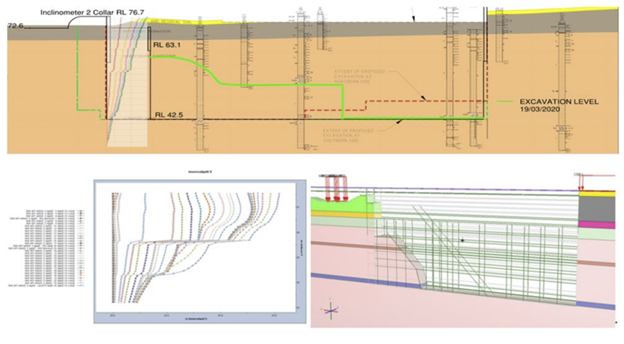
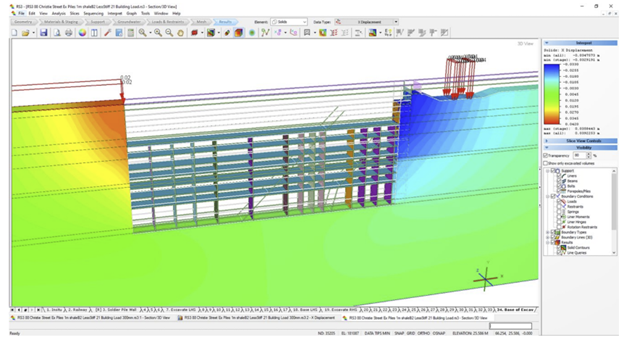
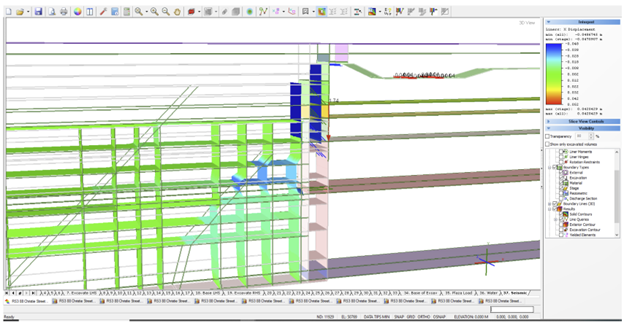
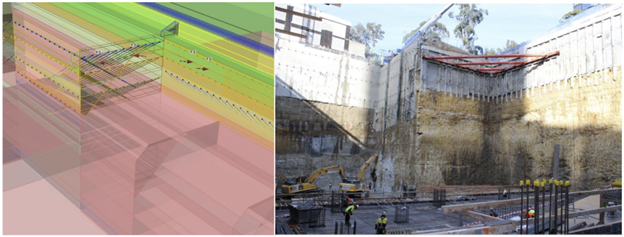
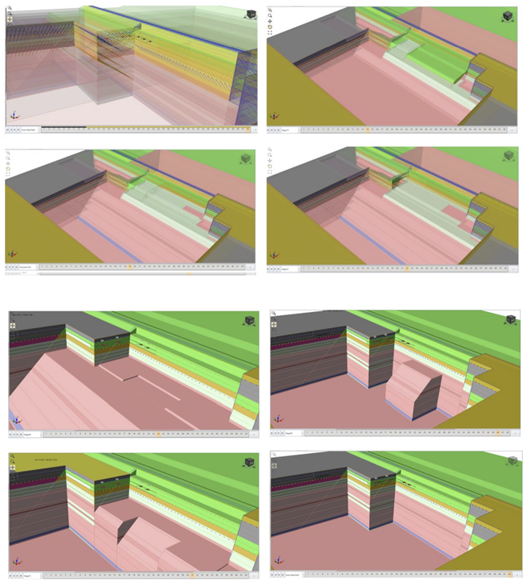
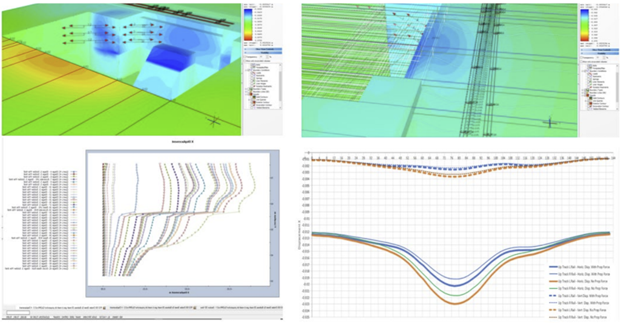
Monitoring & Risk Management
During construction, the excavation walls were monitored through instrumentation and regular visual observation. The maximum measured horizontal wall movement was 28 mm at the mid-point of the west wall, as seen in Figure 12, which was representative of the results generated in RS3.
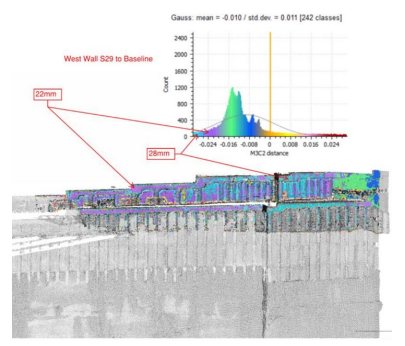
Conclusion: Successful assessment of basement excavation in RS3
This project highlights the significance of RS3’s finite element analysis in assessing the impact between underground infrastructure and high-rise building foundations/deep basement excavations. This study also concludes the advantage of having FEM as a primary tool in the observation-based approach to make accurate predictions and back-analysis to overcome geotechnical challenges.
We recommend reading the full paper for more details.