Finite and Infinite Relief Well Design for Dams and Levees with RS3
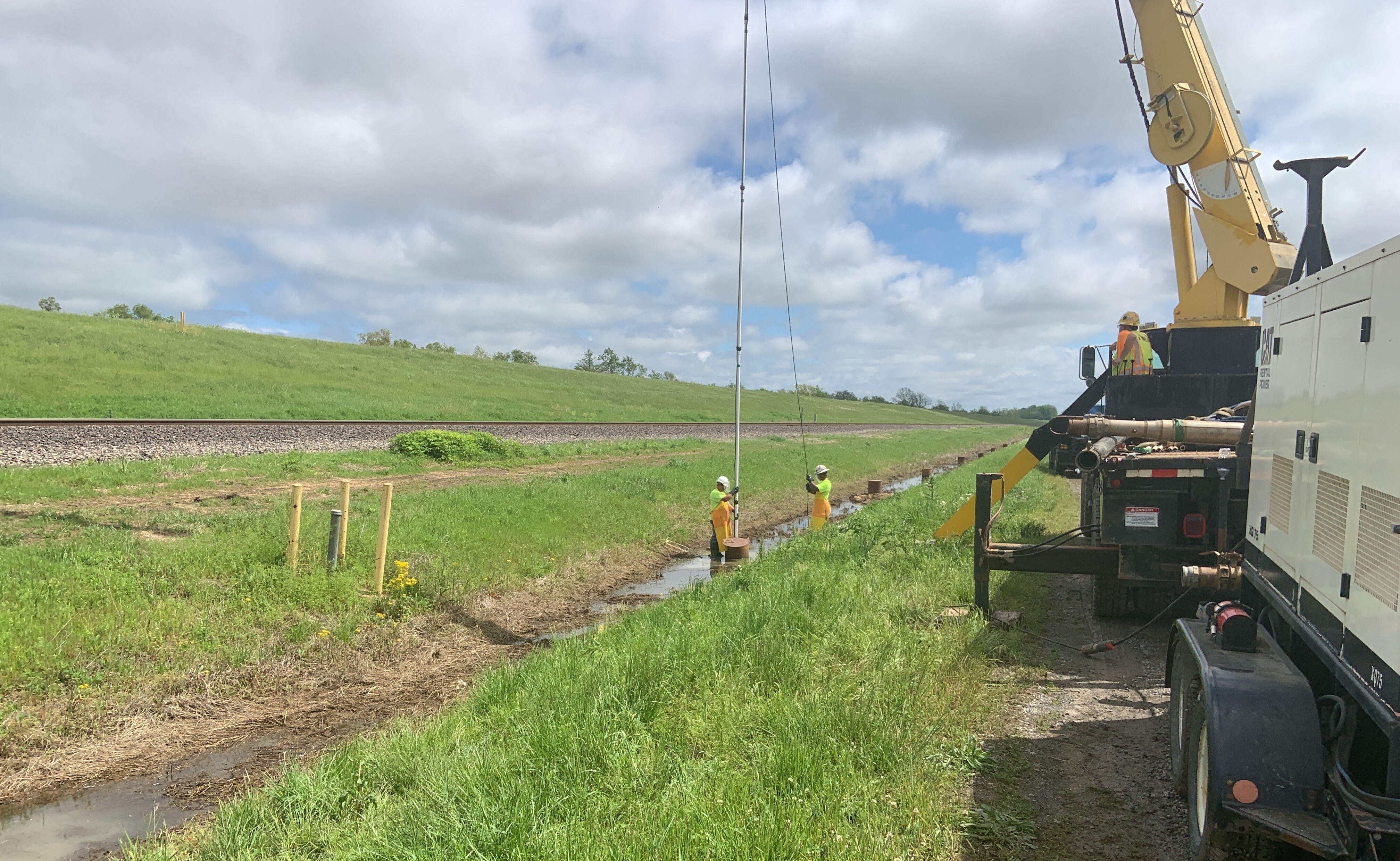
The U.S. Army Corps of Engineers (USACE) is renowned for its engineering expertise, ranging from constructing military facilities, to environmental conservation and flood risk reduction, and they recently further researched finite and infinite relief well design to solve the following two scientific challenges:
- Predicting hydraulic heads in infinite relief well systems more accurately (often simplified in traditional theoretical models) under real-world conditions. Traditional theoretical models assume simplifications, such as a single homogeneous stratum with constant soil permeability.
- Modeling and understanding the effects of finite well line lengths on pore pressure distribution and seepage control, where existing methods fall short due to their reliance on infinite line assumptions.
RS3, the Rocscience 3D finite element analysis software for complex geotechnical models, was a helpful tool in the USACE’s research. Here, we'll explore how detailed simulations in RS3 led to new design methodologies and uplift factors, which can significantly improve the safety and longevity of crucial hydraulic structures such as dams and levees.
For the full research methodologies and findings, you can read the papers on dams and levees considering infinite well design from Keffer and Guy and on finite line relief system design from Keffer, Guy, and Grote.
We will briefly describe the research challenges and the solutions attained using RS3.
RS3 for Infinite Relief Well Design:
Research Challenge: The challenge in traditional infinite relief well design revolves around managing underseepage in large hydraulic structures like dams and levees. Historically, these designs have relied on theoretical models having some simplifying assumptions, which often do not capture all the complex real-world behaviors of water flow beneath these structures. Through initially obtaining matched solutions between analytical models and RS3 3D models for simplified cases, and then using RS3 to consider additional complexities not possible with theoretical or 2D FEM approaches, more accurate estimation of hydraulic pressures can be possible. The findings then can potentially lead to reducing the number of structural failures.

RS3's Solution: RS3 provided an accurate and realistic simulation environment. Using the software’s geotechnical 3D finite element analysis capabilities, USACE engineers could model the infinite well lines with greater precision in terms of the head landward of the well line (existing analytical models to date have assumed landward head to be equivalent to average head). Specifically, RS3 was used to simulate various scenarios under different geological and hydraulic conditions, including layered geologic strata and varying degrees of soil permeability.
In the study, the researchers utilized RS3 to develop the metric, θd, known as the landward uplift factor (see Figure 2), which is used to quantify the maximum hydraulic head occurring landward of the relief wells. This measurement was achieved by conducting detailed finite element simulations that modeled the hydrodynamic interactions and pressure distributions around the well lines. RS3 allowed the researchers to observe and analyze the variations in hydraulic head under various geological and operational conditions, leading to a better understanding of how different well configurations affect pressure on the landward side.
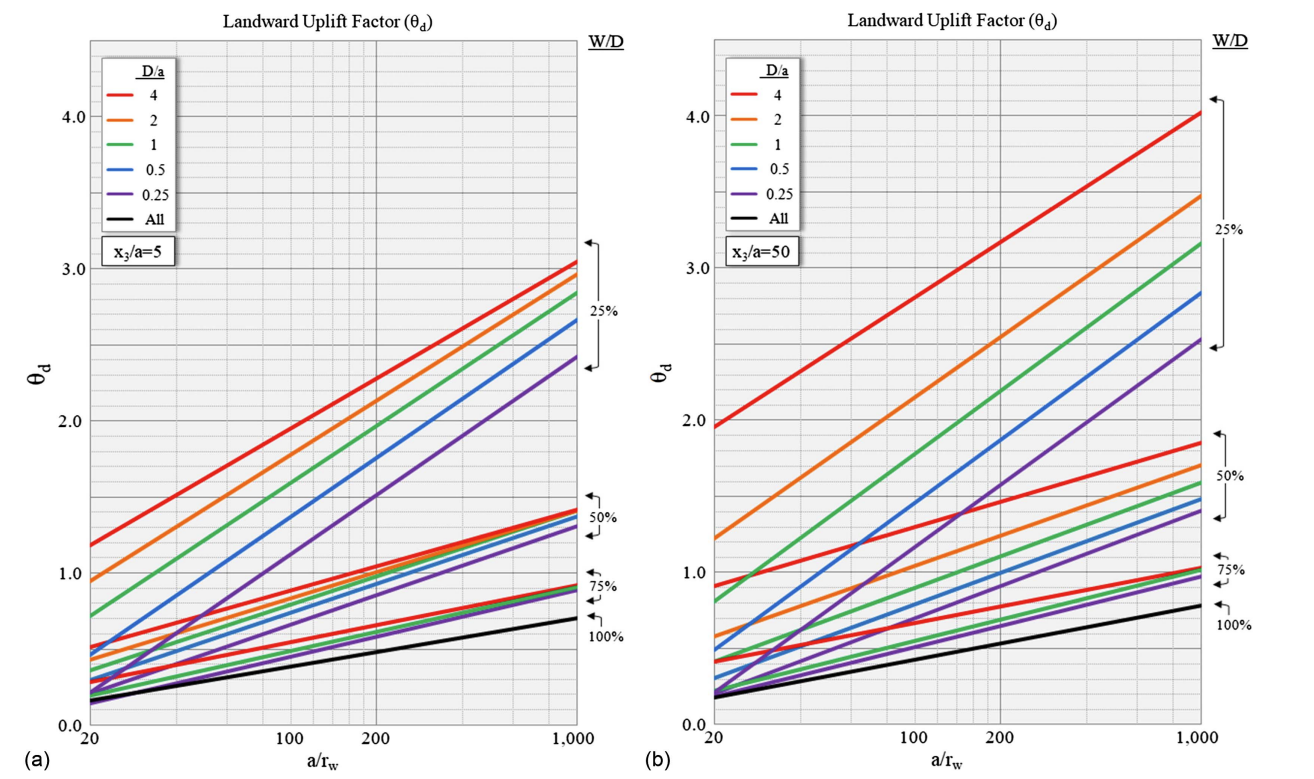
The software enabled detailed visualization and analysis of the water flow and pressure distribution. It integrated complex boundary conditions and variable hydraulic properties across the model, which provided a deeper understanding of the potential impact of these factors on well line performance.
RS3 for Finite Relief Well Design:
Research Challenge: The traditional design approach for relief wells often assumes an infinite well line, simplifying calculations but not accurately reflecting conditions where well lines are finite. This situation can lead to underestimating hydraulic heads, especially at the ends of the well lines where pressure variations are most pronounced, and at the center of the well line as well if infinite solutions are incorrectly used to represent finite systems. These inaccuracies in how finite lines are evaluated can pose risks to the structural integrity of dams and levees, as they may not adequately address the real pressures these structures face. Figure 3 shows how the different head distributions for finite and infinite lines lead to underestimating excess head.
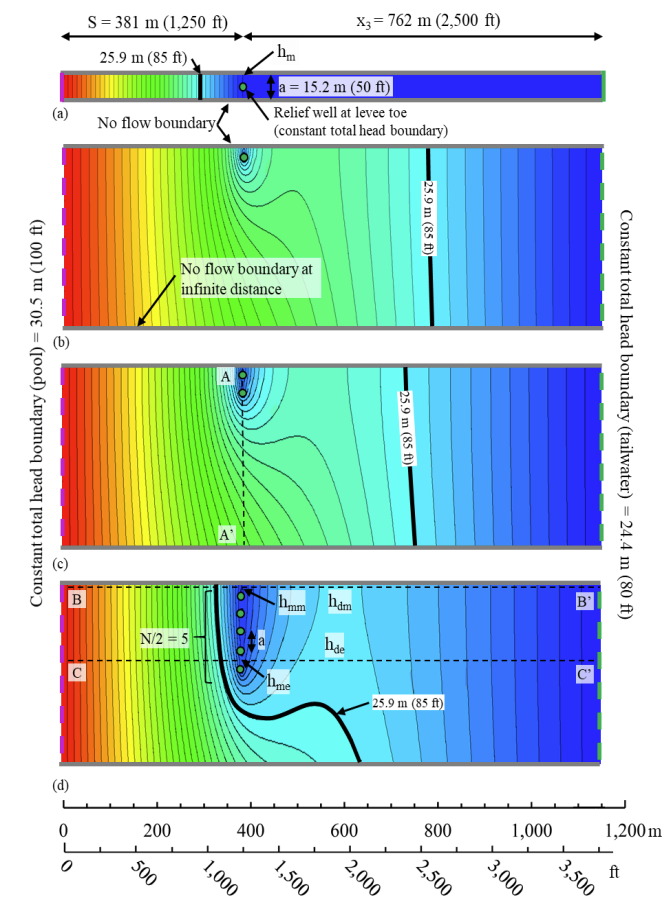
RS3's Solution: RS3 could simulate finite relief well systems under realistic conditions. The software's capability to model complex three-dimensional groundwater flow and interaction with well structures enabled a detailed examination of how hydraulic heads vary along and at the ends of finite well lines.
The software provided the means to incorporate varying soil properties and water levels into the model. These tools enabled the analysis of how these factors influence pressure distributions along and at the ends of well lines — areas known for problematic pressure buildup. RS3’s ability to simulate these detailed interactions helped identify the specific conditions under which traditional infinite line assumptions fail.
By using RS3, researchers could accurately measure how different well configurations, spacings, and lengths influenced the effectiveness of underseepage control measures. This modeling provided invaluable data for refining well designs and ensuring they are more accurately tailored to each project site's specific geotechnical and hydraulic realities.
Key Takeaways from the Research:
Below are the most significant conclusions from the finite and infinite relief well design research that USACE conducted using RS3.
Improved Accuracy in Underseepage Analysis: RS3 helped achieve a highly accurate simulation of underseepage through and beneath hydraulic structures like levees and dams. For simple cases, RS3's advanced finite element modeling allowed for accurate calculations of hydraulic heads and flows, demonstrating less than 5% discrepancy compared to the results of traditional analytical methods.
Cost-Effective Well System Design: Using RS3 helped researchers optimize well spacing and depth (W/D ratio), which demonstrates potential cost reductions in relief well installation without compromising the effectiveness of underseepage control. The modeling capabilities provided by RS3 showed how changes in well system design parameters affect the performance, facilitating more economical designs.
Development of a New Metric (θd): The infinite relief well study led to the creation of a new uplift factor, θd, that specifically addresses the maximum head landward of the wells (hd). Conventional calculations use hav, instead. RS3 was crucial in simulating the conditions under which this new metric becomes relevant.
Detailed Analysis of End Effects in Finite Well Lines: RS3 was instrumental in analyzing end effects in finite well systems, an aspect overlooked in traditional infinite line assumptions. The software enabled detailed observations of increased hydraulic heads at well line ends, leading to the creation of specific uplift factors (θmm, θme, θdm, and θde). This observation enhanced the accuracy and effectiveness of designs for non-infinite well lines.
Integration of Complex Boundary Conditions: RS3 was critical in incorporating complex boundary conditions, such as variable seepage entries and exits, typical of real-world scenarios. This modeling capability was vital to accurately assessing the impact of these conditions on hydraulic heads along and past the well lines.
Overall, RS3 proved a valuable tool for the USACE in relief well design research.
Want to Use RS3 For Your Research? Here’s More That RS3 Can Do:
- Multi-Stage Analysis for Tunneling and Excavations: RS3 allows for the simulation of sequential construction, which enables realistic modeling of stages in tunneling and excavation projects and helps assess the impact of each stage on overall structural stability.
- Integrated Shear Strength Reduction Method: RS3 includes a fully automated shear strength reduction method for slope stability analysis. This method allows one to locate critical failure points and calculate the associated factors of safety for various geotechnical structures.
- Comprehensive Material Modeling Options: RS3 facilitates detailed analysis of soil and rock masses with a wide array of elastic and plastic material models. More modeling options mean more accurate predictions of geotechnical behavior under varied conditions.
- Advanced Stress and Deformation Analysis: With RS3, you can perform detailed stress and deformation analyses to understand the behavior of soil and rock under various load conditions. This analysis is crucial for ensuring the stability and safety of structures like tunnels, retaining walls, and foundations.
- Dynamic Analysis: The software allows for analyzing seismic effects and other dynamic loads on soil and rock structures, providing critical insights for earthquake-resistant design and assessment.
If you want to try the software, click here to start your free trial!