How Cost-Efficient Are the Crab Orchard Mine’s Roof Bolts? RS2 Has an Answer

Researchers studying Tennessee’s Crab Orchard Mine set out to understand just how effective the mine’s current roof bolting strategies really were.
Reece Kurre and Gabriel Walton turned to RS2 to evaluate the mine’s bolting patterns and if they were providing adequate support. Specifically, they modelled and studied the mine’s two distinct roof bolting patterns: a more widely used 1.5 x 1.5-meter pattern, and an intensive 0.8 x 0.8-meter pattern in areas with challenging roof conditions.
Using RS2, the team determined whether the intensive pattern for hazardous areas was necessary or if the standard pattern could ensure roof stability across the mine. We’ve outlined the key takeaways below, and for the full story, you can read the research paper here.
The Geological Setting
Lhoist North America’s Crab Orchard Mine is an underground limestone mine in Tennessee beneath a 244-meter-high mountain. It operates using the room and pillar method, each measuring 15 x 15 meters. The mining height is capped at 15 meters to maintain a pillar width-to-height ratio of 1:1. Excavation is done in two stages: a 9-meter-tall top heading followed by a 6-meter-tall bench, with at least 9 meters separating the two levels.
The limestone formations here are generally strong but come with challenges; the mine’s roof is susceptible to sub-horizontal cracks and stress-induced fractures caused by blasting, which complicates ground support requirements. These cracks are often undetectable until after blasting and can lead to sudden instability in the roof, so a bolting strategy that can adapt to varying conditions within the mine is key. But how elaborate does the bolting need to be?
The Research Challenge
The standard 1.5 x 1.5-meter bolting pattern has been the backbone of roof support at Crab Orchard Mine and has proved effective in most areas. But in sections with hazardous conditions — like those with visible joint separation or large unstable ledges from blasting — a more intensive 0.8 x 0.8-meter pattern was used. Despite addressing severe roof challenges, this pattern can come with significant time and cost implications.
The challenge was clear: was this more intensive pattern truly necessary, or could the standard pattern support the mine’s most problematic areas? It’s an important question because over-engineering leads to unnecessary costs and delays, while under-engineering could jeopardize safety.
The Solution
The research team used RS2 to build detailed numerical models that accounted for the mine’s complex geology. These models included key parameters such as the uniaxial compressive strength (UCS) of the limestone, Young’s modulus, and Poisson’s ratio, all derived from laboratory testing. Joint persistence was based on jointing patterns and crack distributions within the rock mass. The Hoek-Brown failure criterion simulated the rock mass behavior, and a discrete fracture network was incorporated to represent the jointing and cracking patterns observed.
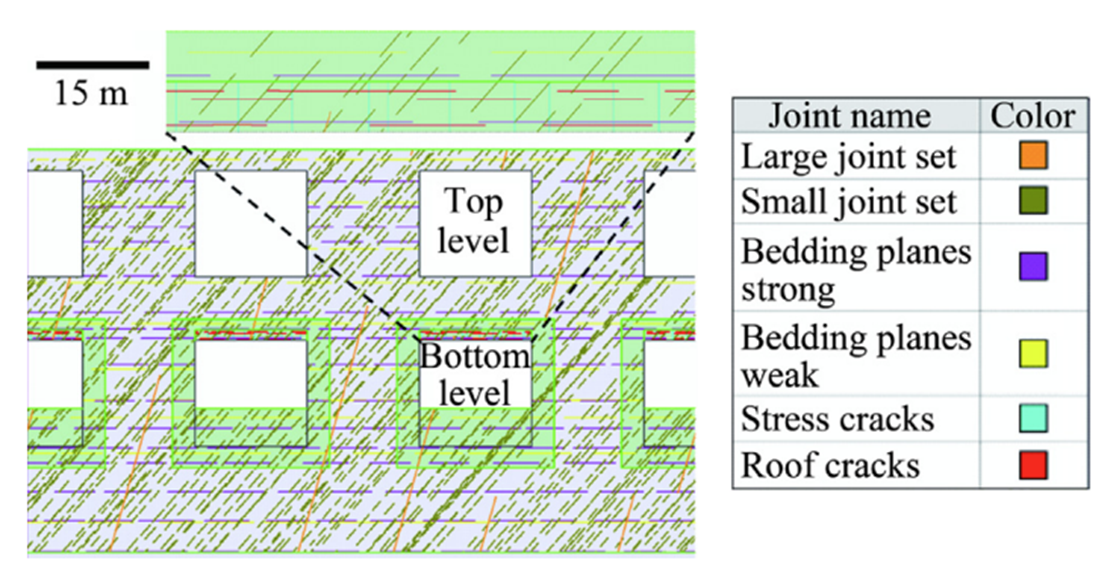
RS2 also allowed the team to perform staged excavation modeling so the different bolting patterns could be assessed over time as the excavation progressed. With this approach, researchers had a dynamic view of how the roof might behave under various support scenarios and insights into the mine’s long-term stability.
The Results
The standard 1.5 x 1.5-meter pattern performed well and maintained safety factors above the critical threshold of 1.5 – even in areas with significant jointing and roof cracks.
Interestingly, the models showed that the standard pattern could also adapt well to varying joint persistence and friction angles, with only minor increases in displacement observed under the most extreme conditions.
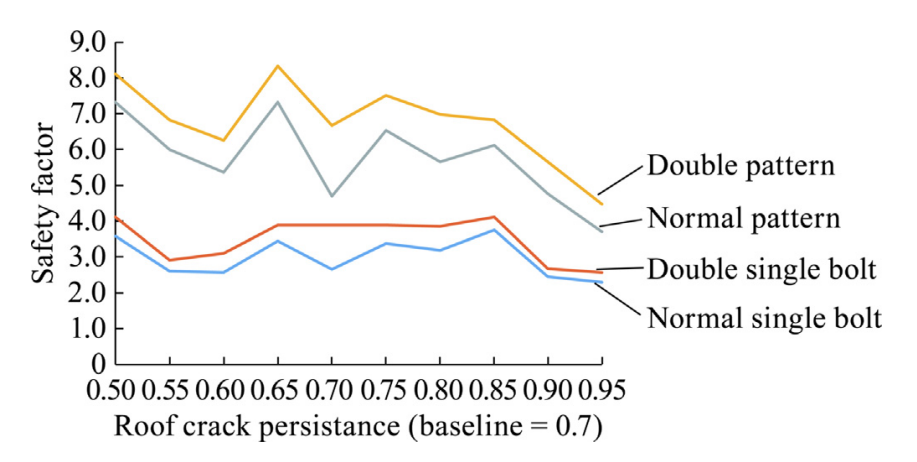
On the other hand, the more intensive 0.8 x 0.8-meter pattern did provide additional stability, particularly in scenarios with highly persistent roof cracks and low friction angles. But the improvements were marginal when compared to the increased effort and cost of installation.
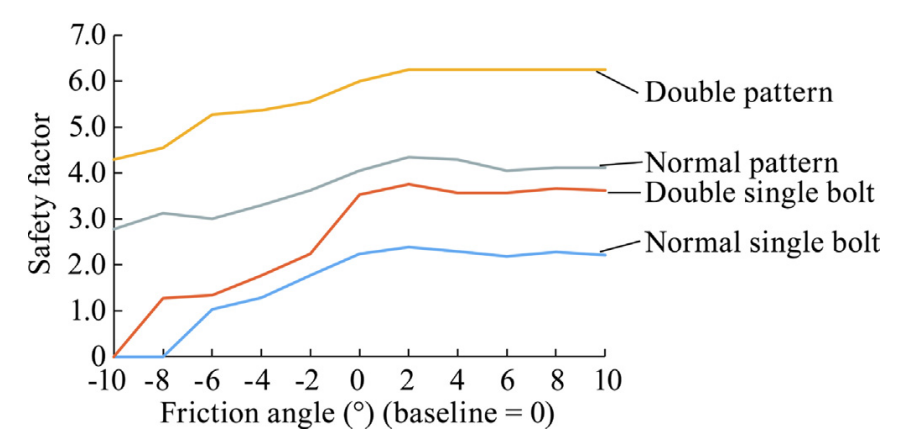
As seen in Figure 3 above, reducing the friction angles below their baseline values resulted in a gradual decrease in safety factors for all scenarios, as more joints experienced shear failure, causing an increase in bolt loads. Conversely, raising the friction angle above the baseline had minimal impact on the safety factors. There was no significant change in the number of joints yielding, and consequently, the load on the bolts remained consistent.
Figure 4 below shows that although there was a slight variation in displacement between the baseline and the best-case scenario (10°), the number of yielded joints remained largely unchanged.
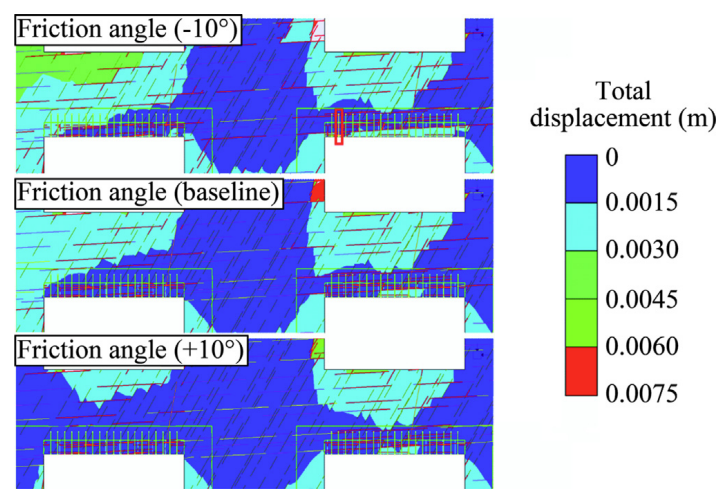
The Verdict
The research conducted at Lhoist Crab Orchard Mine used several numerical models powered by RS2. The findings all suggest that the standard 1.5 x 1.5-meter pattern, when properly applied and monitored, is sufficient to ensure roof stability across most of the mine. Safety factors below the design value of 1.5 were only seen in a few extreme test cases involving individual bolts.
The methods shown in the research highlight how engineers can allocate resources more efficiently and focus on the intensive bolting pattern where it is genuinely needed and reduce unnecessary operational costs. Other underground mines can apply a similar approach to evaluate their own bolting patterns using RS2 to simulate scenarios and optimize support systems based on site-specific conditions.
Frequently Asked Questions
What are the common causes of roof instability in underground mines?
Roof instability can be caused by geological features like weak rock layers, the presence of joints and fractures, and high in-situ stress. The risk of roof falls and safety hazards can be worsened by blasting operations, improper roof bolting patterns, and dynamic loading.
What is mine roof bolting and why is it important?
Mine roof bolting involves installing steel rods, or bolts, into the roof of an underground mine to stabilize the rock and prevent roof collapses. It is a critical ground support method that enhances the safety of mining operations by reinforcing the roof, distributing loads, and securing loose rock masses. Effective roof bolting reduces the risk of accidents and improves the longevity of the mine.
What are the different types of mining roof bolts, and what factors should you consider when selecting bolts for different rock types?
Mechanically anchored bolts, resin-grouted bolts, cable bolts, and friction bolts can all be used in underground mines, and each has its own strengths. Mechanically anchored bolts use expansion shells to grip rock. Resin-grouted bolts rely on a chemical adhesive to bond the bolt to the rock. Cable bolts are perfect for deep-seated stabilization because they’re long and flexible. Friction bolts provide support through radial pressure within the drill hole.
You should consider the rock's strength, jointing, and fracture patterns, in-situ stress conditions, and the bolt’s expected load when making your choice. Resin-grouted can be better for weak or fractured rock while mechanically anchored bolts are more apt for stronger rock. You should also consider groundwater and long-term stability requirements throughout your thought process.
What is the optimal spacing for roof bolts in a room and pillar mining method?
The optimal spacing for roof bolts in room and pillar mining depends on the geological conditions, roof rock strength, and the mine’s layout design. Spacing typically ranges from 1 to 2 meters. The standard pattern at Crab Orchard Mine is 1.5 x 1.5 meters, but this can be adjusted based on the specific stability needs found through numerical modelling and ground control analysis.
Which Rocscience software solutions can help me with my mining projects?
We offer a range of geotechnical software solutions for mining projects:
- RS2 is ideal for 2D finite element analysis of ground support systems and provides stress distribution, stability, and deformation insights.
- RS3 offers 3D modelling capabilities and allows for more comprehensive analysis of complex geological structures, including mine slopes, tunnels, and open pit mines.
- RocTunnel3 determines valid block formations by intersecting joints in 3D space and calculates the factor of safety, and it’s valuable for assessing tunnel stability and support design in underground mining and civil engineering projects.
- Slide2 is a 2D slope stability analysis program that evaluates potential failure surfaces using limit equilibrium methods. It’s great for analyzing pit slopes, embankments, and mine waste dumps, whether they’re simple or complex.
- Slide3 is our 3D slope stability tool that analyzes complex geometries and spatial variability in material properties, perfect for detailed pit slope designs and landslide assessments.
- Dips helps with stereographic analysis of structural data, so that engineers can visualize and interpret orientation data from discontinuities, joints, and faults.