How RS2 Validated a Proposed Tunnel Support System Under the Himalayan Peaks

What’s the secret to keeping tunnels stable in the towering Himalayas, the youngest and tallest mountain range on Earth stretching across South Asia? A 672-meter adit tunnel in the complex terrain of the Garhwal Lesser Himalaya, India, required meticulous analysis and innovative solutions for stability.
The interplay of rock mass behaviour, geological variability, and in-situ stresses posed challenges that traditional methods like the rock mass rating (RMR) and Q-systems couldn’t fully address. Although these frameworks provide a valuable starting point, they fall short of addressing critical responses such as deformation, stress redistribution, and plastic zone extents.
In this case study, we’ll cover how RS2, through detailed modelling of stress distribution, deformation, and support interaction, bridged this gap and helped determine that the recommended designs met the demands of the environment. For the full scope of the project, including tables and figures, you can read the original research paper by Md Alquamar Azad, A. K. Naithani, Saurav Shekhar, Seraj Ahmad, and S. K. Singh.
The Geological Setting
The 672-m adit tunnel, part of the Rishikesh-Karnaprayag rail line, cuts through the Berinag Formation of the Garhwal Lesser Himalayas. The rock mass is dominated by quartzite, with colours ranging from cream to light pink and deep purple, interspersed with dark phyllites. These formations are intricately folded and fractured by major thrusts such as the main boundary thrust (MBT) and tons thrust (TT), meaning that the geology is highly variable and significantly impacts tunnel stability.
The region’s structural complexity results in rock mass quality values ranging from Class III (fair) to Class V (very poor). In addition, adverse geological occurrences like river-borne deposits and road-cutting material introduce weak overburden layers and zones of instability.
The Research Challenge
Geotechnical assessments identified several challenges, including fractured and unstable rock masses and varying groundwater conditions, to overcome. While empirical methods like the RMR and Q-systems provided an initial framework for designing tunnel support, they could not account for the following critical aspects:
- Extents of the plastic zones around the excavation.
- Stress redistribution in weak zones or areas with high overburden.
- Ability of the reinforced shotcrete to withstand bending moments and axial forces.
Numerical modelling was needed to validate the proposed support designs more fully and to address the site's specific challenges.
The Solution
First, input parameters like the Geological Strength Index (GSI), Uniaxial Compressive Strength (UCS), and stress ratios were derived from field investigations and lab testing. Then, the engineers defined the tunnel geometry, excavation sequence, and external boundaries. Using RS2, they built models that subdivided the problem domains into fine triangular meshes to calculate stress and deformation accurately.
The models incorporated support elements such as shotcrete, rock bolts, and steel ribs tailored to the site's variable rock mass conditions. Critical zones near the portal and Class V rock masses were supported with additional stabilizing measures such as forepoling and grouted zones. A blast damage factor (D) of 0.7 was applied to reflect actual excavation conditions.
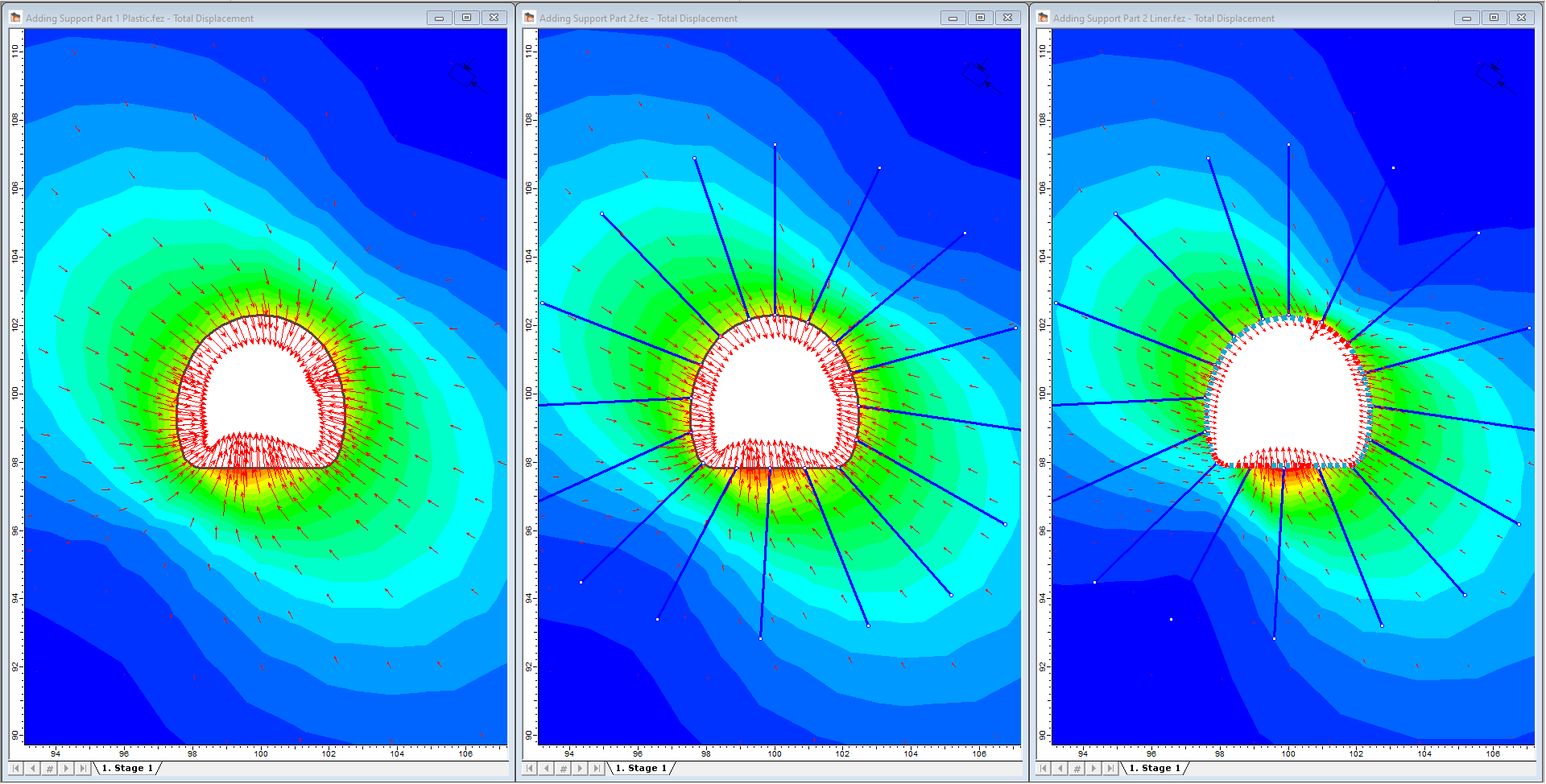
RS2 elastoplastic analysis was used to evaluate the interactions between the support systems and the rock mass, focusing on critical factors such as displacement, stress patterns, and the capacity envelopes of the reinforced shotcrete. An M-N curve was used to assess how well the shotcrete could withstand bending moments and axial forces under various conditions. Overall, the analysis showed that the proposed support systems were well-suited to the geological setting and could maintain stability and help prevent excessive deformation.
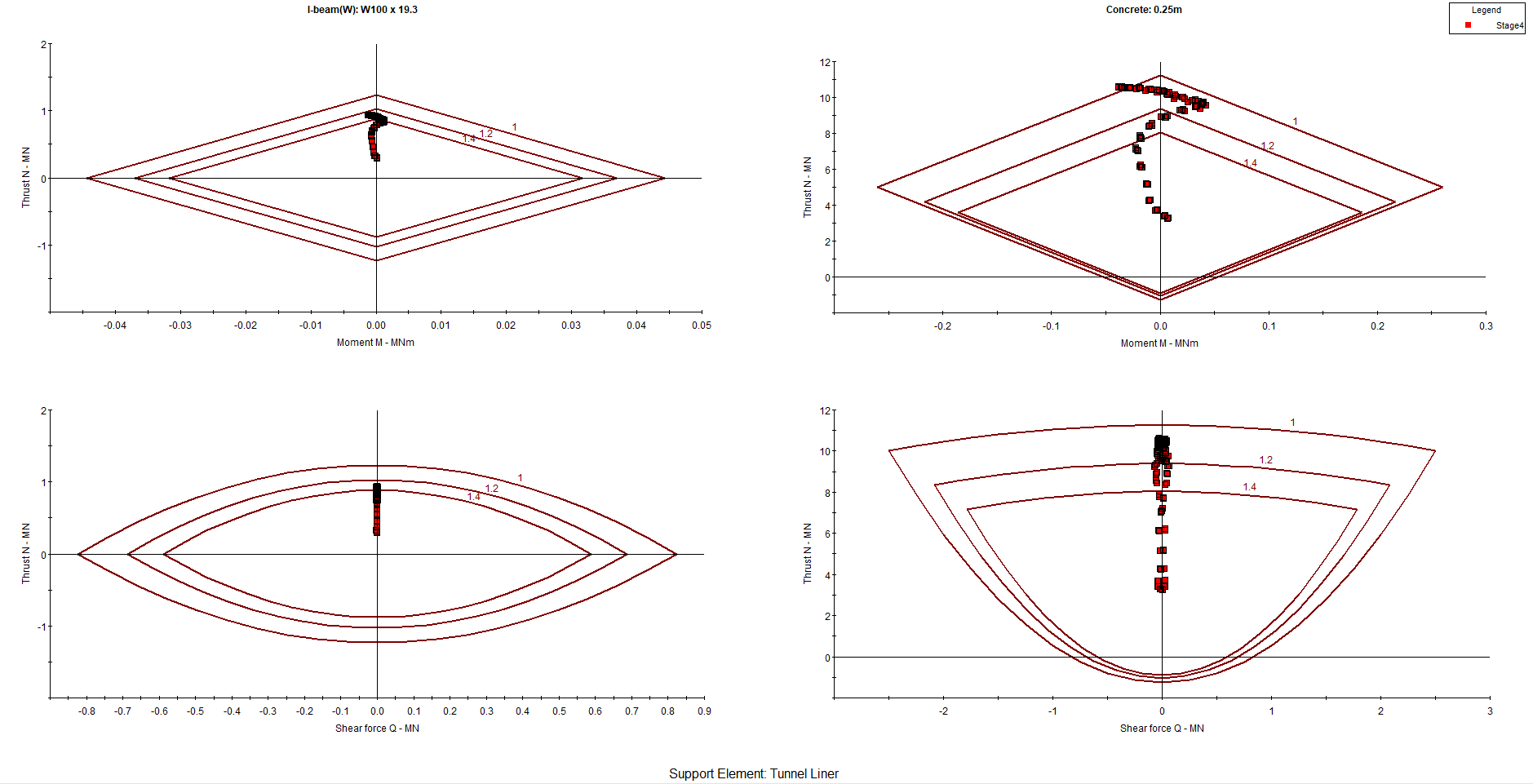
The Results
RS2 provided detailed understanding of tunnel behaviour across varying rock mass categories and overburden heights:
- The plastic zone extents were accurately predicted, clearly showing zones of instability around the tunnel. These details informed support design.
- Displacement measurements ranged from 1.4 mm at the crown to 23.4 mm at the invert, which were all within permissible limits.
- The reinforced shotcrete had a safety factor of 1.2 or higher, validating its ability to resist bending and cracking under all conditions.
It was confirmed that the support system would be safe under the observed geological conditions and applied loads; no significant bolt yielding was observed.
The Verdict
Traditional empirical methods are valuable for preliminary stages, but numerical tools like RS2 can help overcome limitations in stress and deformation analysis. In this case specifically, using our software and incorporating variable geological parameters and real-world boundary conditions helped researchers meet safety and stability requirements. As the demand for infrastructure in challenging terrains like the Himalayas grows, RS2 can help ensure the success of critical geotechnical projects worldwide.
Questions About Tunnel Support Systems, Answered
What are the different tunnel support systems engineers can employ, and what factors determine the choice of support?
There’s a range of tunnel support systems available to engineers, including shotcrete, rock bolts, lattice girders, steel ribs, and forepoling. Often, more than one support type is employed to provide stability in variable or weak rock masses.
Your choice should consider factors like rock mass quality, groundwater conditions, in-situ stress levels, and excavation methods. Areas with weak rock masses or high deformation may need stronger support systems such as steel ribs or shotcrete, while stable rock mass zones might need minimal reinforcement. You can read our tunnel lining tutorial here for more details.
What tunnel excavation methods are there, and when should you use them?
Tunnel excavation methods include the New Austrian Tunneling Method (NATM), drill-and-blast techniques, and mechanical methods like tunnel boring machines (TBMs). Each method is suited to specific geological conditions and project requirements.
NATM is ideal for geologically complex regions like the Himalayas, as it uses the surrounding rock mass as a natural load-bearing structure and allows for flexible adjustments to support systems during construction. Drill-and-blast methods are commonly employed for hard rock and regions with variable geology, where they can offer precise excavation control. TBMs are efficient for uniform and stable rock masses, but they can be less reliable in highly fractured or unpredictable conditions.
Why is plastic zone thickness essential in tunnel analysis?
Plastic zone thickness around a tunnel affects excavation stability and indicates the degree of rock deformation in immediately surrounding zones. It helps engineers understand where the rock mass transitions from stable to unstable, guiding the placement and design of support systems to ensure tunnel stability and safety. Numerical modelling tools like RS2 can accurately predict plastic zone thickness and provide insights that empirical methods cannot. Such numerical analysis is critical for preventing excessive deformation and optimizing support systems in geologically complex environments.
How does groundwater affect tunnel stability?
Groundwater can reduce rock mass strength, cause seepage issues, and increase deformation. Effective drainage systems and waterproofing techniques are essential to mitigating these adverse effects, especially in regions with variable groundwater conditions like the Himalayas.
How do rock mass classifications like RMR and Q-systems impact tunnel design?
The RMR and Q-systems provide a framework for assessing rock mass quality and selecting initial support designs. However, although these classification systems guide engineers in determining excavation methods and reinforcement needs, they often require numerical validation for more accurate decision-making.