Optimizing Elliptical Shaft Design With RS2 and RS3
Elliptical shafts are a space-efficient solution for deep excavations, however their asymmetric geometry creates unique stress distributions. RS3 and RS2 together can help you find critical stress redistribution insights that impact structural stability for better accuracy and safer construction.
Research conducted by J. Werner, G.R. Piazzetta, P. T. Cortizo, and P.T. França examined two modelling approaches — 2D axisymmetric analysis and a fully integrated 3D analysis — to determine the most effective way to analyze and design elliptical shafts. In this case study, we’ll cover how RS2 and RS3 were used in the research, and how they can enhance stress redistribution analysis, refine reinforcement strategies, and optimize excavation sequencing for safer, more efficient shaft construction.
The Geological Setting
The research used a generic elliptical shaft measuring 22 m by 18 m in diameter and 20 m in depth, with a primary shotcrete lining of 0.40 m thickness. The geological profile consisted of four distinct soil layers, with different strength, stiffness, and consolidation properties that influenced stress redistribution as the excavation progressed.
The upper layers featured softer soils (c = 10–60 kPa, E = 8–40 MPa), while deeper layers exhibited higher stiffness and shear strength (c = 90–120 kPa, E = 80–100 MPa). These variations significantly impacted shaft deformation patterns, as softer soils contributed to greater displacement and instability around the excavation. Understanding how these varying stiffnesses influenced deformation and load transfer was crucial in developing an accurate design strategy.
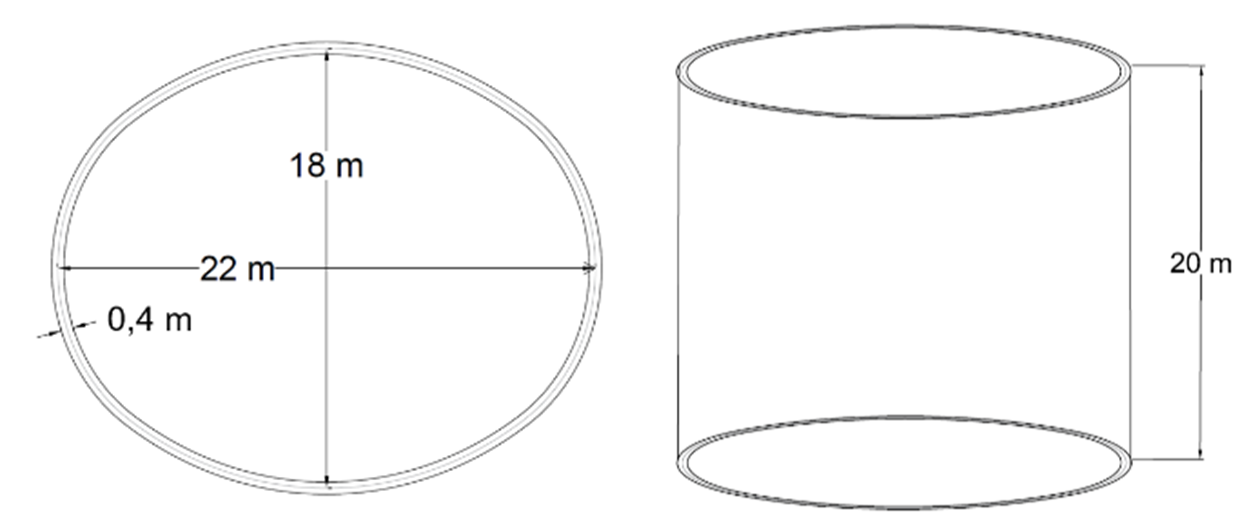
The Research Challenge
Elliptical shafts behave differently from circular ones, due to their varying radii in different directions, which leads to uneven stress distributions. Traditional methods impose radial stresses derived from circular models onto elliptical structures, which may not accurately capture:
- The true interaction between the soil and the shaft lining.
- The progressive redistribution of loads during excavation.
- The increased tensile forces at certain points of the lining.
Over- or under-designing reinforcements is more likely with these inaccuracies and can lead to higher costs or structural vulnerabilities. The challenge was to develop a more accurate and predictive model that could help engineers design elliptical shafts with greater confidence.
The Solution
The researchers modeled the elliptical shaft using two approaches:
Axisymmetric 2D Model (RS2 + SAP2000)
- RS2 was used to simulate soil behavior around a circular shaft, where a uniform radial field stress was assumed.
- The extracted radial stresses were then applied as imposed loads in a 3D structural model (SAP2000), where the shaft lining was analyzed separately using Winkler springs to approximate soil-structure interaction.
- This method simplified stress transfer but did not fully capture excavation-induced load redistribution.
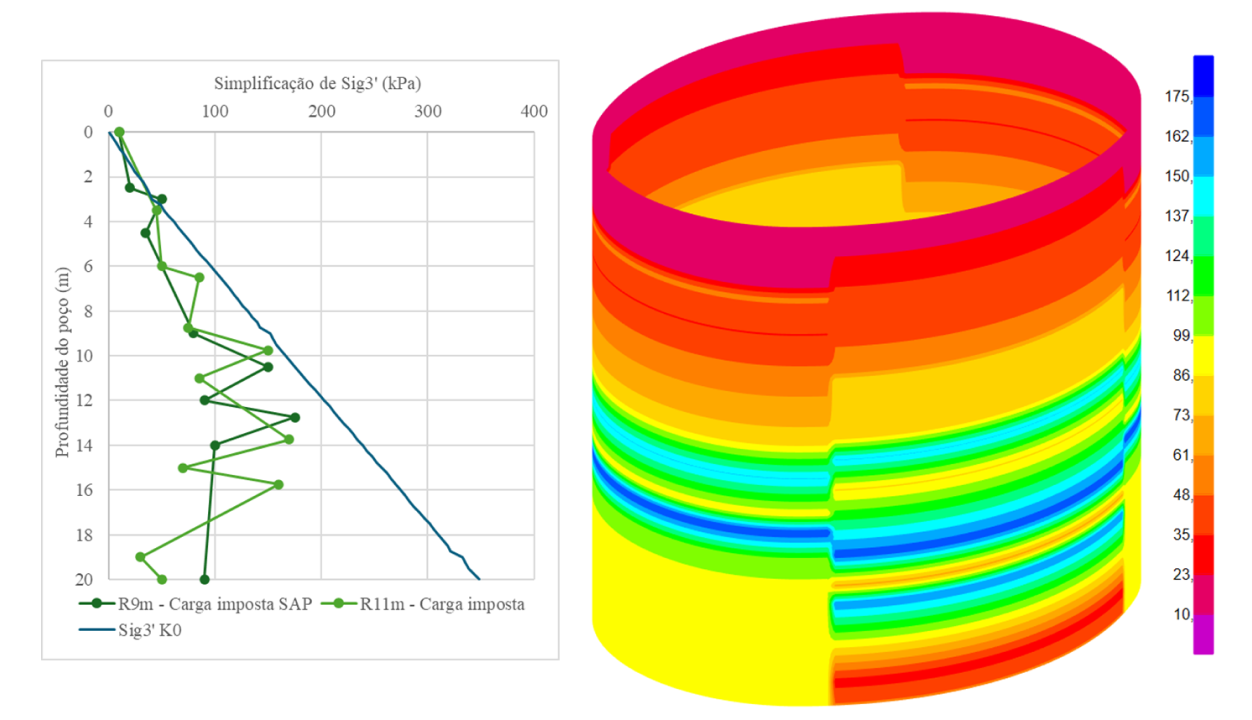
Integrated 3D Model (RS3)
- RS3 was used to create a fully 3D finite element model of the elliptical shaft, incorporating nonlinear material behavior, sequential excavation, and progressive stress redistribution.
- The soil and lining interacted dynamically throughout the excavation process and captured the changes in stress concentrations and arching effects.
- Unlike the 2D approach, the elliptical geometry was explicitly modelled, which allowed for a more precise representation of asymmetrical deformations and differential load paths.
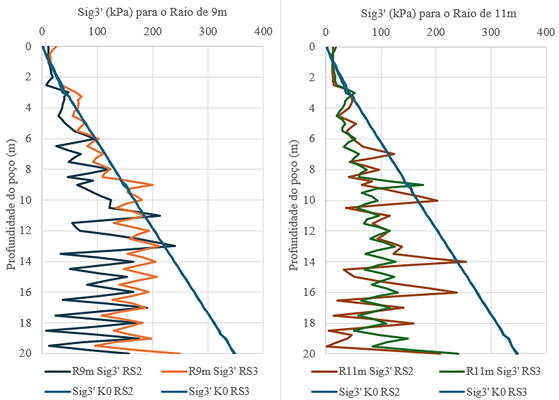
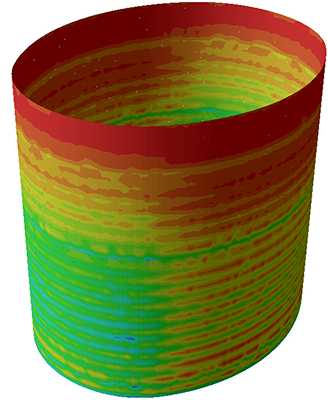
By using RS3, the researchers were able to directly simulate the evolving load transfer mechanisms, eliminating the need for manual stress adjustments between separate models, which often introduce conservative assumptions that do not align with real-world excavation conditions.
The Results
The comparative analysis revealed key differences between the two approaches:
- Stress Distribution: The RS3 model provided a more accurate stress representation, particularly in the minor axis, where the stress redistribution was more concentrated than predicted by the 2D approach. RS3 also revealed arching effects and shear redistribution that were not captured in the 2D model.
- Axial Forces: The vertical axial force was entirely tensile in RS3, whereas the SAP2000 model underpredicted tensile effects, leading to an underestimation of required reinforcement. In elliptical shafts, this can be critical in preventing crack propagation and potential structural failure.
- Bending Moments: The 3D model showed smoother and more realistic bending moment distributions, while the SAP2000 model produced abrupt variations, indicating that simplified assumptions do not capture the progressive nature of excavation-induced stress redistribution.
- Displacement Behavior: RS3 more accurately simulated excavation sequence effects, including soil relaxation, delayed stiffening of the shotcrete lining, and base uplift, which were not observed in the 2D model.
These findings demonstrate that the assumptions made in traditional 2D axisymmetric models can lead to significant discrepancies in force estimation, reinforcement design, and lining behavior, reinforcing the necessity of fully integrated 3D analysis for complex excavation projects.
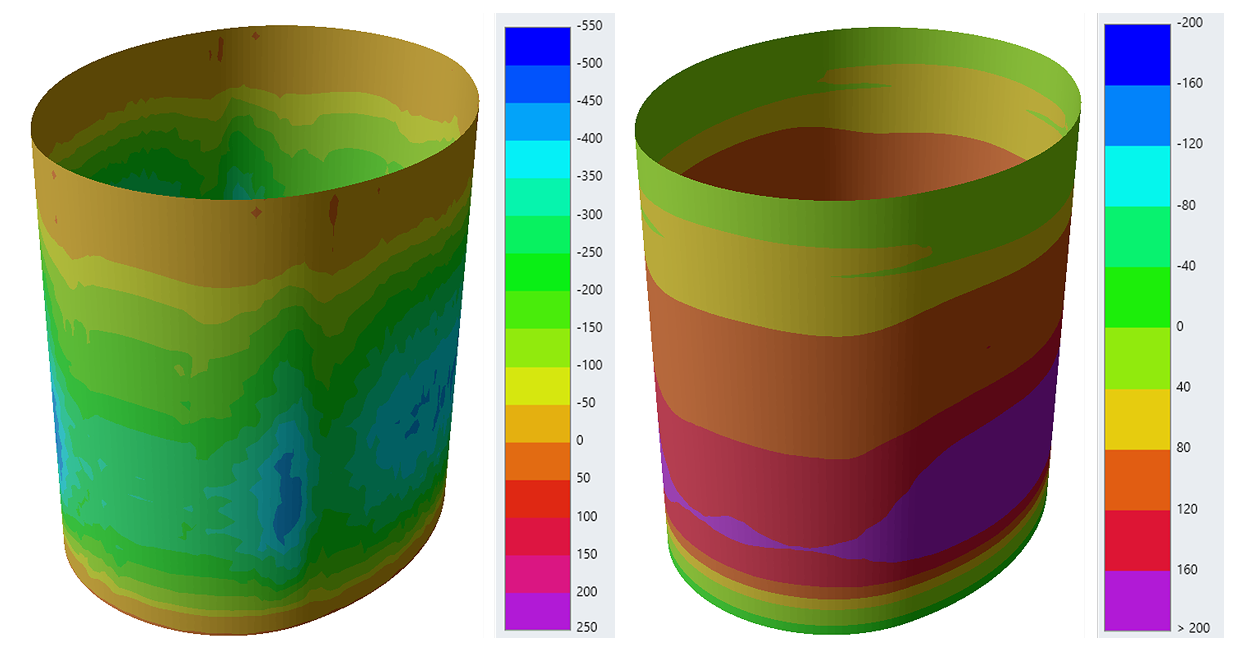
The Verdict
Selecting the appropriate numerical modelling approach is important for elliptical shaft design. While axisymmetric 2D analysis provides a valuable and practical first estimate, a 3D analysis validates and further strengthens the project with captured progressive loading effects, variations in stress fields along the major and minor axes, and realistic bending moment distributions.
Also, simplified axisymmetric assumptions can lead to significant discrepancies in force estimation, potentially underpredicting tensile forces and localized bending moments. For complex geometries like elliptical shafts, a fully integrated 3D analysis provides a more complete representation of excavation-induced deformations and load transfer mechanisms.
By using RS3, geotechnical engineers can:
- Accurately model real-world stress conditions without relying on imposed loads.
- Better optimize reinforcement design, reducing over-design and unnecessary material use.
- Enhance safety by capturing progressive excavation effects that traditional models miss.
Ready to Optimize Your Elliptical Shaft Design?
Your design decisions impact the cost, safety and performance of elliptical shafts. With RS3’s advanced 3D modelling, you can eliminate uncertainties in stress distribution and reinforcement strategies for safer, more efficient excavations. Start your free trial of RS2 and RS3 today.
Learn More About Elliptical Shaft Design:
What is soil-structure interaction, and why is it important?
Soil-structure interaction (SSI) refers to the way excavation-induced stresses in the surrounding soil mass influence the structural response of the shaft lining and vice versa. In elliptical shafts, stresses are not uniformly distributed, leading to higher loads on the minor axis and potential asymmetrical deformations. Proper SSI modelling ensures accurate stress predictions, optimized reinforcement, and minimized risk of structural failure.
How does the elliptical shape of a shaft affect soil-structure interaction compared to a circular shaft?
Elliptical shafts do not distribute stresses symmetrically like circular shafts. The major axis tends to deform more, while the minor axis experiences higher compression due to uneven confinement. This results in differential stress redistribution, varied bending moments, and localized reinforcement demands, making 3D numerical modelling essential for accurate design.
What is the Winkler model, and how is it used in shaft design?
The Winkler model represents soil as independent springs that resist deformation based on a defined stiffness coefficient. In shaft design, it is used to approximate soil pressure on the lining in structural analysis software like SAP2000. However, it simplifies soil behavior by ignoring stress redistribution and arching effects, making it less accurate for elliptical shafts compared to full 3D numerical modelling.
What are the main challenges in designing elliptical shaft linings?
The biggest challenges include:
- Uneven Stress Distribution: Higher loads on the minor axis require localized reinforcement.
- Variable Bending Moments: Differing curvatures along the major and minor axes affect structural response.
- Excavation-Induced Deformations: Soil relaxation and load transfer require staged reinforcement.
- Numerical Modelling Limitations: Axisymmetric 2D models may underestimate stress variations, making 3D modelling crucial for accurate predictions.
How do bending moments vary in elliptical shaft linings compared to circular ones?
In circular shafts, circumferential bending moments are more uniform, as stresses are evenly distributed. In elliptical shafts:
- The major axis tends to flex outward, creating tensile stresses on the outer face.
- Moment variations are more pronounced, requiring differential reinforcement strategies for structural stability.
How does excavation impact stress redistribution in deep shafts?
During excavation, the removal of soil alters the stress equilibrium, triggering:
- Arching effects, where soil stresses redistribute around the opening.
- Lateral stress relaxation, causing inward displacements in unsupported sections.
- Progressive load transfer to the lining, requiring staged reinforcement to control bending and axial forces.
- Accurate 3D modelling of excavation sequences is essential to prevent excessive deformations and ensure lining integrity.
How do bending moments in an elliptical shaft compare to a circular one?
Elliptical shafts experience non-uniform bending moments due to their shape:
- More localized bending in the minor axis, leading to higher shear demands near sidewalls.
- Greater moment fluctuations along the perimeter, requiring a more complex reinforcement layout than circular shafts.
Want to design and analyze more realistic elliptical shafts? Try RS2 and RS3 today!
Start Free Trial