Smarter Meshing, Faster Results: Try RS3's Hybrid Mesh Feature
Waiting hours for your slope stability analysis to compute? Meshing is a critical and potentially lengthy step in geotechnical finite element analysis (FEA) for accurate simulations, but RS3’s Hybrid Mesh feature makes the process more efficient.
Traditionally, choosing between linear (4-node) tetrahedral elements and quadratic (10-node) tetrahedral elements can present a trade-off: 4-node elements solve faster but can struggle with accuracy in areas with high displacement gradients. 10-node elements improve precision but increase computation time and memory use.
Instead, you can selectively apply higher-order elements only where needed with RS3, so that both accuracy and a lower computation time are achieved. Here, we’ll cover key concepts about Hybrid Mesh that Dr. Sina Moallemi (Product Manager of RS3) and Dr. Arsalan Jameei (Geomechanics Specialist at Rocscience) discussed in 2024 and show you how to use it for better modelling.
Understanding Finite Element Choices: 4-Node vs. 10-Node Elements
FEA software traditionally provides two main element types:
Method |
4-Node Tetrahedral Elements (Linear) |
10-Node Tetrahedral Elements (Quadratic) |
Computation Speed |
Faster. |
Slower. |
Accuracy |
Lower. |
Higher (due to quadratic interpolation). |
Ideal For |
Simulations with limited memory or when speed is a priority. |
Capturing complex displacement gradients. |
When modelling complex geotechnical problems, engineers historically had to balance solution accuracy with computational efficiency, however Hybrid Mesh resolves this challenge.
How Hybrid Mesh Works
Hybrid Mesh applies higher-order (10-node) elements only in regions where displacement gradient is higher, while the rest of the model remains linear (4-node). This targeted refinement provides accurate results while optimizing solver performance.
The key technical challenge when mixing element types is ensuring solution continuity between high-order and low-order regions. RS3 resolves this using the Master-Slave elimination method, which mathematically integrates the mid-side nodes of 10-node elements into the surrounding 4-node mesh. This ensures compatibility between elements and prevents gaps or overlaps in the deformation response.
Application in Slope Stability Analysis
In the webinar, Hybrid Mesh was tested on a 3D slope stability model using the Shear Strength Reduction (SSR) method. The results were compared across three meshing approaches:
Method |
4-Node Elements (Linear) |
10-Node Elements (Quadratic) |
Hybrid Mesh (4-Node + 10-Node in critical regions) |
Computation Speed |
Faster. |
Slower. |
Fast, slightly longer than 4-node. |
Factor of Safety |
1.79 (overestimated). |
1.61 |
1.61 |
Notes |
Limited accuracy. |
High accuracy. |
Balanced accuracy and speed. |
This example confirmed that you can achieve the accuracy of higher-order elements while significantly reducing processing time.
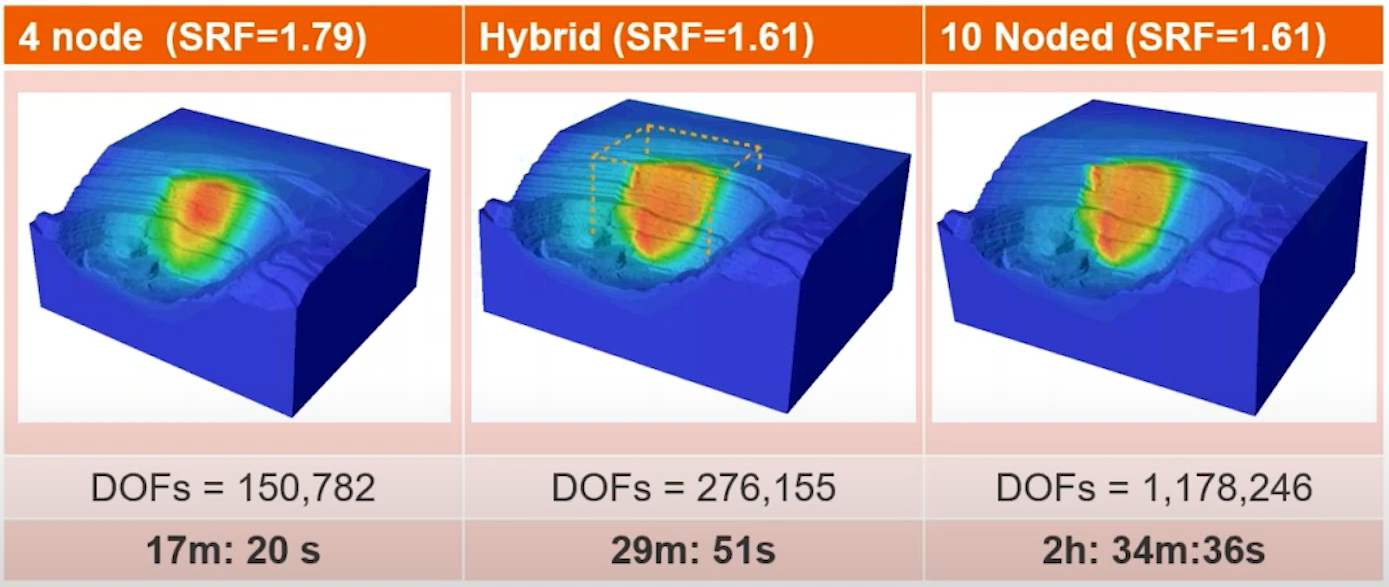
Application in Tunnel Excavation
The benefits of Hybrid Mesh were further highlighted in a tunnel analysis example. Using a sequential excavation model, engineers analyzed:
- Yielded zones around the tunnel.
- Liner bending moments and circumferential forces at critical sections.
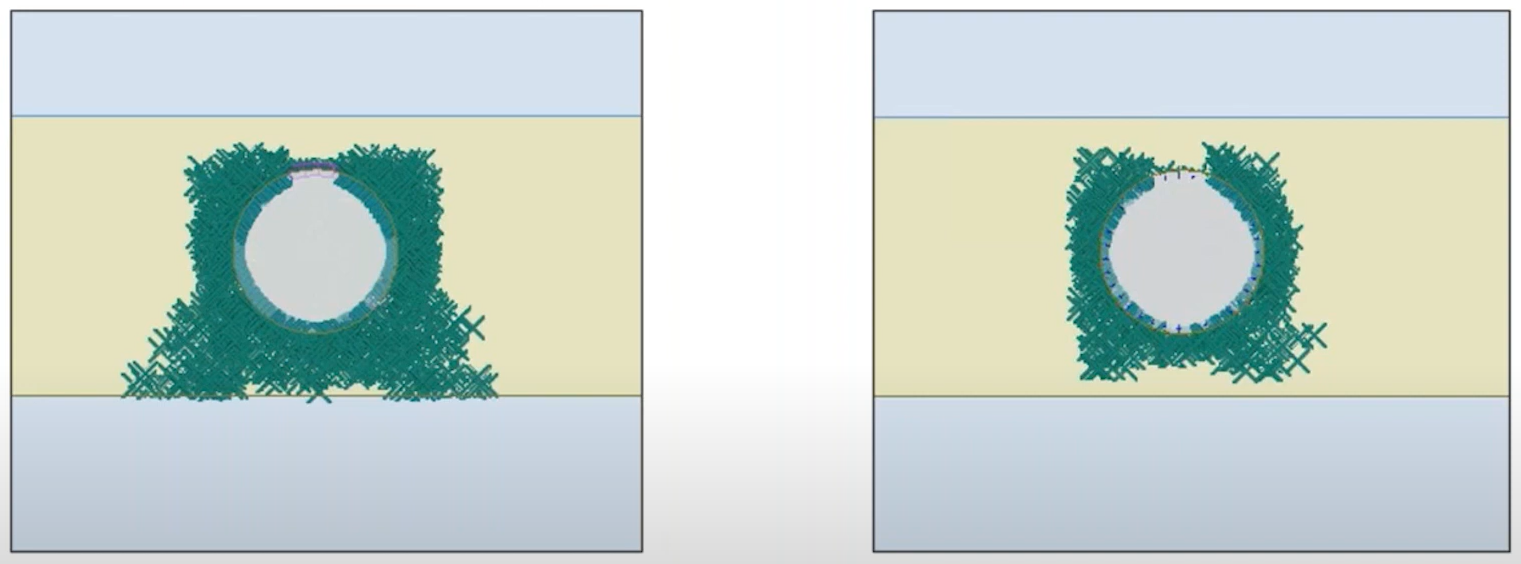
Results showed that using only 4-node elements underestimated deformation and bending moments, while 10-node elements provided more accurate stress distributions but increased runtime. The Hybrid Mesh approach captured stress concentrations correctly, with minimal performance impact.
Additionally, increasing the density of 4-node elements (to mimic 10-node accuracy) led to only marginally better results while drastically increasing computation time. Hybrid Mesh provided a more efficient alternative.
When to Use Hybrid Mesh
Hybrid Mesh is most effective when:
- Localized accuracy is required: For example, in tunnel linings, slope failure surfaces, and stress concentration around excavations.
- Memory limitations prevent full 10-node modelling: Hybrid Mesh keeps models within practical hardware limits.
- Computation time is a concern: You can mesh large-scale models without excessive processing delays.
The webinar showed that you can achieve the same accuracy as a fully 10-node mesh while significantly reducing computation time, so it’s ideal for most large-scale geotechnical simulations.
Key Takeaways
Whether you're working on large-scale slope stability models or tunnel excavations with complex stress distributions, Hybrid Mesh ensures that you can:
- Refine accuracy where it matters: By applying higher-order elements only in critical regions, you can avoid unnecessary computational load.
- Optimize slope and tunnel analyses: You can capture localized stress concentrations without over-meshing the entire model.
- Ensure compatibility across element types: The Master-Slave elimination method maintains seamless transitions between 4-node and 10-node elements.
- Get reliable results, faster: Hybrid Mesh achieves the same accuracy as fully 10-node models but in much less time.
By adopting a targeted meshing strategy, you can run larger, more complex simulations without sacrificing accuracy or efficiency.
Ready to see Hybrid Mesh in action?
Start a free trial of RS3 today to put Hybrid Mesh to the test on your own models to experience faster, more accurate geotechnical analysis.
Start Your Free Trial