Validating Bored Pile Defects in Malaysia With RS3
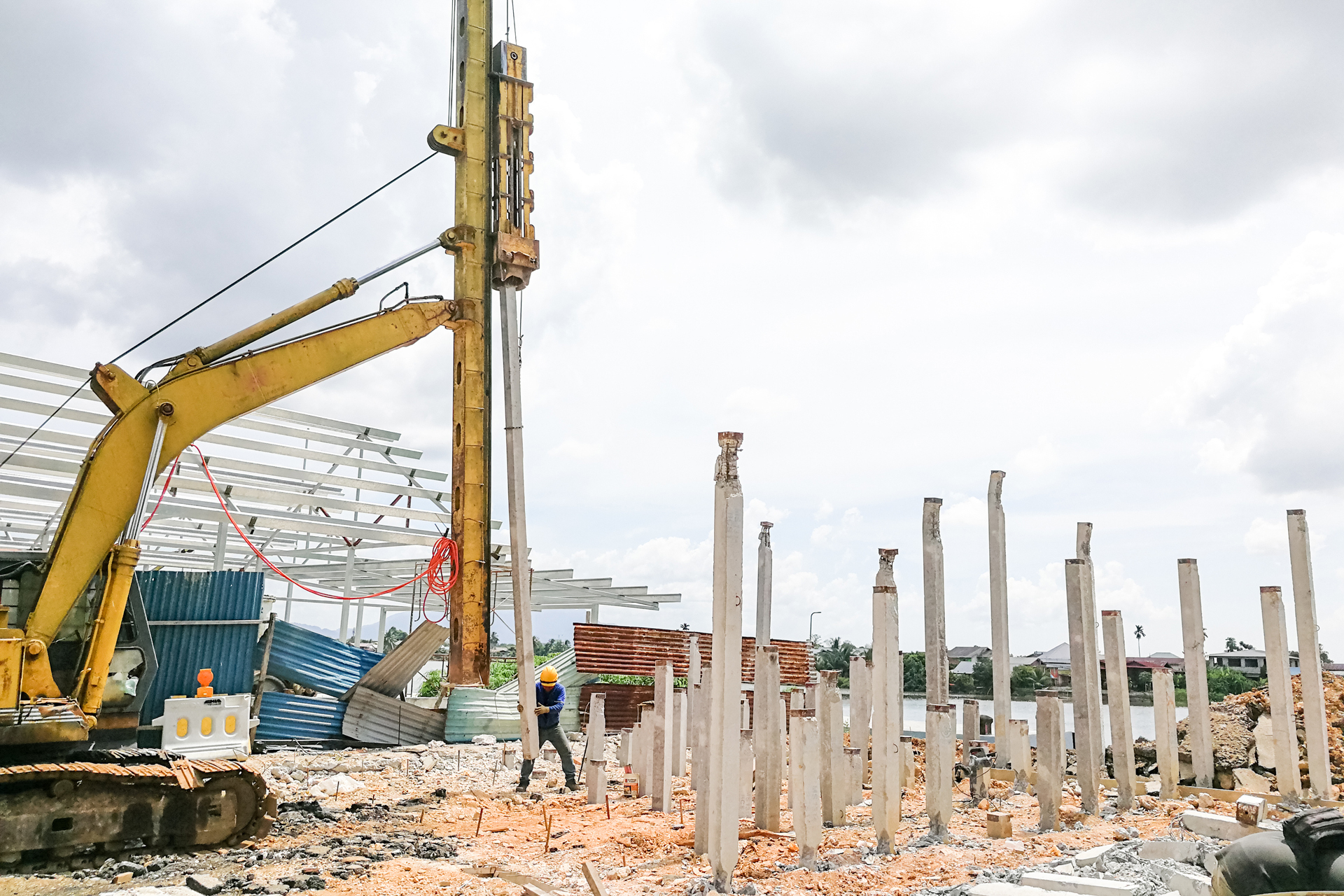
What if advanced sensing technology could uncover bored pile defects? Distributed optical fibre strain sensing (DOFSS) can measure complete strain profiles and load transfer along a pile shaft, which offers a powerful tool for detecting anomalies such as necking, bulging, and concrete contamination.
But validating these findings with real-world data is essential to understand its accuracy. In a recent study, researchers A. A. A. M. Beddelee, H. Mohamad, and B. P. Tee used RS3 to analyze detailed strain data and simulate and validate pile behavior under various conditions.
Two specific bored piles were selected for this study, based on their strain profiles and the presence of suspected common defects such as necking and bulging. These projects, located in Kuala Lumpur and Selangor, involved pile load testing on bored piles using DOFSS. Read on to learn how RS3 accurately simulated the conditions and validated the research findings.
The Geological Setting
The research paper focused on two specific projects in Malaysia, each with its own distinct geological contexts that posed a challenge for pile integrity. The first project was in Kuala Lumpur, with a test end-bearing pile with a diameter of 900 mm and a length of 32.5 m. The soil stratigraphy consisted of 13 layers, primarily composed of sandy silt, sandy clay, silty sand, and sandstone, with the groundwater table at a depth of 3 meters. The pile was socketed into sandstone at a depth of 27 meters.
The second was in Selangor and had a test shaft-bearing pile with a diameter of 1200 mm and a length of 31.8 m. The soil layers included sandy silt, silty sand, and gravelly silt, with hard strata encountered beyond 27 meters. The groundwater table was at a depth of 3 meters.
The Research Challenge
The primary challenge was to validate the hypothesis that DOFSS could detect defects in bored piles using field data. The Kuala Lumpur pile was expected to have necking and bulging defects along the shaft, while the Selangor pile was thought to have concrete contamination. The task was to simulate these field conditions and compare the strain profiles from DOFSS with those generated in the simulations to confirm the defects.
Traditional methods of pile integrity testing often fall short due to their inability to provide continuous strain profiles along the entire length of the pile, so this research aimed to demonstrate that DOFSS could offer a more reliable and comprehensive solution for identifying pile defects. Additionally, ensuring that the simulated strain profiles closely matched the real-world data required calibration, iterative adjustments, and extensive analysis to fine-tune the parameters for each unique setting.
The Solution
RS3 was used for 3D FEM simulations of the bored piles, so that the DOFFS findings could be validated. The process began with a detailed setup of the simulation environment and incorporated geological data and pile specifications from the field. Each simulation aimed to replicate the real-world conditions as closely as possible. Below are a few reasons why RS3 was the best solution:
- Precise Modelling: RS3 can incorporate complex shapes and variations in dimensions, including for suspected defects like necking and bulging. The software's user-friendly interface is helpful for creating detailed 3D models, which would ensure every aspect of the pile structure was accurately represented. See Figure 8 in the original research paper for an example of the orthographic projection for the Kuala Lumpur bored pile in RS3.
- Visualization Capabilities: RS3’s powerful visualization capabilities would allow researchers to visualize strain distribution along the pile in three dimensions, making it easier to identify and understand the impact of defects. See Figure 3 in the original research paper that shows the strain along the Kuala Lumpur bored pile distributed using the optic strain sensor.
- Advanced Analysis Tools: By diving deep into the strain data, RS3 can help identify patterns and anomalies indicative of pile defects. These tools would make it possible to simulate the exact conditions that led to the observed strain variations, providing a clear picture of how defects affect the pile's performance.
The Results
The results of the RS3 simulations were consistent with the findings, which validates the hypothesis that DOFSS can detect pile defects accurately. Below are some specifics from each pile. Below are some specifics from each pile and see Figure 9 in the original research paper for a simulation of the Kuala Lumpur bored pile and Figure 12 for the Selangor pile.
- Necking of the Kuala Lumpur Pile: RS3’s simulation showed strain increases at depths where necking was suspected and closely matched the field data. The differences were slight, with strain values differing by only 0.9-3.7% (the strain at depth D1 (2-8.1 m) was 420.06 µm/m in the RS3 model compared to 436.25 µm/m in the field data).
- Bulging of the Kuala Lumpur Pile: The simulation identified a bulging defect with a strain decrease at the expected depth. The excess concrete volume was accurately represented in the RS3 model. The bulging region observed from numerical analysis of RS3 was confirmed by matching the field strain profile at depth D3 (12-14 m).
- Concrete Contamination of the Selangor Pile: Because of the concrete contamination, the strength and stiffness of the pile was reduced. Using the updated concrete properties in RS3, the obtained results were very close to the sensor data, and the RS3 model confirmed the extent of contamination, extending beyond the initially expected 3 meters to 5 meters.
The field data showed strain values beyond the design strain of 0.00125 m/m, with the highest strain at 0.002 m/m, which was accurately reflected in the RS3 simulation. Concrete core samples taken from 0-3 m depth showed reduced compressive strengths of 25.5 MPa, 23.1 MPa, and 10.4 MPa, supporting the presence of reduced stiffness due to contamination.
The Research Conclusions
- RS3 accurately replicated the field strain profiles and confirmed the presence of necking, bulging, and concrete contamination defects. The close match between simulated and field data shows the reliability of DOFSS.
- The actual concrete stiffness was lower in the simulations than the designed values, which means engineers should be careful during design and validation. With the Selangor pile, for example, the stiffness varied significantly due to contamination.
- Taking an iterative approach in RS3 allowed for refined predictive modelling. By adjusting material properties and pile geometries iteratively, RS3 ensured the simulations closely matched real-world data.
The Verdict
RS3 is a valuable tool for modelling piles under different geological and environmental conditions. The calculated results were in close agreement with those obtained from optical strain fibers placed along the pile. By accurately simulating real-world conditions and validating research findings, RS3 can provide reliable and actionable insights into pile integrity.