FAQs
- What coefficients of restitution should I use?
- For a lump mass analysis, why do rocks with different masses have similar paths? Shouldn’t heavier rocks bounce back up higher or have longer run out?
the governing equations for motion is straight kinematic projectile, in which mass is not used; and
the lump mass impact theory uses mass on both sides of the equation, so mass cancels out.
- How many rocks should I throw down the slope? How do I know how many to throw to get a representative analysis?
- What’s the difference between Lump Mass vs. Rigid Body analysis? Which one should I use?
- How does shape in Rigid Body analysis affect the path?
- Under what scenario would a rock have non-zero initial velocity? How do I determine what initial velocities to use?
- Why are the rock paths shown above the slope for rigid body analyses?
- Why do the bounce heights appear very large for rigid body analyses?
- What is the Rn scaling function and where do the scaling factors come from? Is there a reference?
Coefficients of restitution range from 0 to 1. A coefficient of 1 is only applicable to perfectly elastic materials. Following slope impact, the rock would bounce back with the same speed/height (i.e., no energy loss). On the other hand, using a coefficient of 0 assumes perfectly inelastic materials. Following slope impact, the rock would not bounce back.
For values of Rn and Rt, the materials library is a starting place (Slope > Slope Material Library > Common Types…). This library provides reference values with corresponding citations. However, coefficients of restitution should always be calibrated to the site, given availability of testing or historic data.
For the lump mass method, with everything staying the same except for the rock mass, rocks of different masses should have the exact same bounce height and runout distance. This is because:
In other words, though a heavier rock has larger kinetic energies throughout the path, it also has a larger mass to propel itself out after impact. The only source of damping comes from the coefficients of restitution. To include the effects of mass on damping, scaling Rn by Mass can be applied (Analysis > Scaling Functions > Select Scale Rn by mass).
For the rigid body method, the effect of mass can be observed when slope roughness is introduced into the analysis. Smaller rocks tend to get trapped in local valleys, whereas larger rocks can overcome the local undulations and reach longer runout distances.
The number of rocks to throw can depend on how sensitive the analysis is to the number of rocks. The user could perform a sensitivity analysis to determine a representative number. In addition, if a wider range of statistical distribution is applied to material and seeder properties, then a larger sample (i.e., a greater number of rocks) is recommended.
The lump mass analysis follows the method developed by Pfeiffer and Bowen (1989) and assumes the rock is a point/particle. Energy is conserved in the governing equation. As rock shape is not accounted for, the outbound angular velocity is calculated from an equivalent radius derived from the user inputs for rock density and mass. In the lump mass analysis, the coefficients of restitution are velocity based (V’n = -Rn * Vn).
The rigid body analysis assumes the rock is infinitely rigid and rock shape is explicitly accounted for in the analysis. The 2D impact theory is based on Stronge, and the coefficients of restitution are energy based (not velocity based). The current rigid body impact theory in RocFall2 does not use a tangential coefficient of restitution. The only source of tangential dampening during impacts is friction. We have observed that, in some cases, friction alone is insufficient to slow down the rocks, so we added an option to apply CRSP tangential dampening if the user chooses (Analysis > Project Settings > General > Rigid Body).
An introduction to rockfall analysis theories can be found here (applicable to RocFall2 and RocFall3):
The rock shape can have a number of effects. Shapes introduce eccentricity/moment arm from the centre of mass (COM) to the contact point. Depending on the impact geometry, angular velocity can be introduced upon impact. Shapes also affect where the rock impacts the slope, as illustrated in the following figure. The trajectory of the rock that has shape (on the right) would be affected by the wall. Shapes can also affect whether the rock can slide or roll. Sliding, toppling, or rolling can be observed in a rock with shape, whereas a rock modelled as a point in lump mass analysis can only slide.
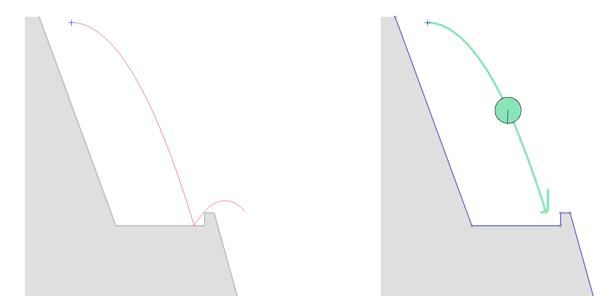
Non-zero velocities can stem from vibrations (e.g., earthquakes or anthropogenically induced, such as blasting). These velocities could be monitored in the field, or if uncertain as to what values to use, then a statistical distribution can be applied to the horizontal, vertical, and/or rotational velocity.
For 2D rigid body analyses, calculations for the trajectory are performed at the rock centre of mass (COM). Translational and rotational velocities are both calculated at the COM, and these quantities form the basis for contact point velocities.
When using Rigid Body analysis, we recommend enabling Rn scaling (Analysis > Project Settings > Rigid Body > Select either Scale Rn by Velocity or Scale Rn by Mass, but not both). Rn is the only source of dampening in the direction normal to the slope. Based on experience, the Rn scaling factor helps to produce more realistic results (such as bounce heights).
The Rn scaling function is used to scale down the Rn for rocks impacting at larger velocities or for rocks of larger masses. A scaled down (or smaller) Rn value means greater damping. This is applicable for modeling the additional energy loss incurred in high energy impacts, where the slope deforms or the rock locally fractures. The scaling factors K and C represent the velocity and mass at which Rn is reduced by half, respectively. K and C should be in the same unit system as the project settings.
Reference: Pfeiffer, T.J. and Bowen, T.D. (1989). Computer Simulation of Rockfalls. Bulletin of the Association of Engineering Geologists Vol. 26, No. 1, pp. 135 to 146